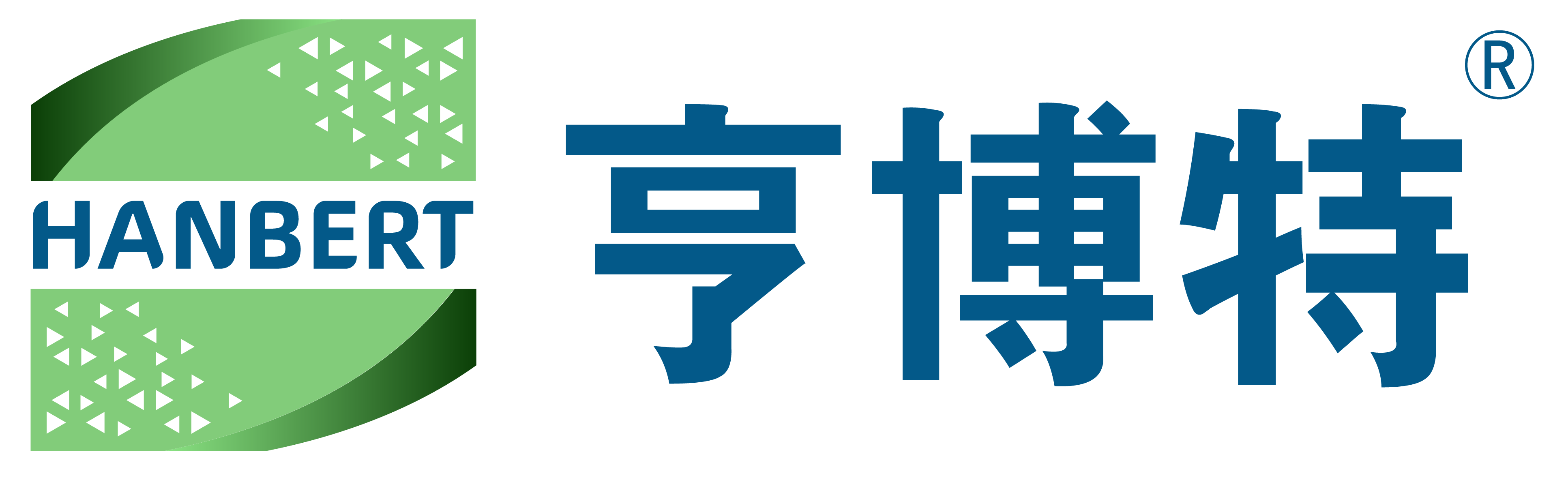
Summary::
Tailored welded plate stamping technology is one of the important measures for lightweight automotive currently. The application of this technology can reduce vehicle weight, reduce costs, and reduce pollution. It is currently widely used in the production of the automotive industry. This article introduces the welding process involved in aluminum alloy welding and stamping technology, analyzes the stamping performance, influencing factors, and existing research progress of aluminum alloy plate welding and stamping plates. Finally, it introduces the current application status and future development prospects of welding and stamping technology in the automotive industry.
1 Introduction
As the energy crisis, environmental pollution, global warming and other issues continue to intensify, human beings are facing a series of survival crises, and countries around the world are actively making efforts. In 2020, China proposed the goal of "striving to reach the peak of carbon dioxide emissions by 2030, and striving to achieve carbon neutrality by 2060". As an effective means to reduce carbon emissions and achieve carbon neutrality, lightweight technology is one of the most important research and development directions in the automobile manufacturing industry. Especially for new energy vehicles, the body weight directly affects the vehicle's endurance mileage, thus affecting its product competitiveness. Aluminum alloy is an ideal lightweight material for replacing steel in automobile body manufacturing. Its related design, processing, forming, and heat treatment technologies in the field of automobile manufacturing are currently one of the hot research directions.
Tailored welded blanks stamping forming is a new process that has gradually gained attention in the automotive manufacturing industry in recent years. It achieves one-time forming of body structural or covering parts with different strength requirements by welding plates of different materials, thicknesses, and strengths into one and then stamping forming them. This reduces the number of sheet parts, simplifies the body structure, reduces assembly steps, improves assembly accuracy, and reduces development costs Reduced the number of mold development, improved the strength of the vehicle body, and reduced the overall weight of the vehicle body [2]. This article focuses on the research progress of aluminum alloy sheet welding technology, sheet stamping forming process, and its application status in the automotive manufacturing industry.
2. Common Methods and Process Characteristics of Plate Welding
In the automotive manufacturing process, many sheet metal stamping parts have different strength requirements for different parts. To avoid increasing the weight of the entire vehicle, different thicknesses or strengths of sheet metal are used for parts with different strength requirements to minimize the design of excess strength. Therefore, according to the traditional manufacturing process, the method of first stamping and then connecting produces a large number of sheet metal parts with different thicknesses, materials, and heat treatment states. The assembly between these parts requires a large number of fastening connectors or later welding connections, which can cause corresponding problems [3]. Among them, the biggest problem with fastener connections is the addition of additional weight and assembly operations, which also require high assembly accuracy and high production costs. The process of forming before welding seriously affects the dimensional accuracy of the parts due to the stress and deformation generated during the welding process, resulting in a high scrap rate and ultimately affecting the assembly and manufacturing cost of the entire vehicle.
Therefore, in order to meet the demand for lightweight manufacturing, the recent car manufacturing process involves welding plates of different materials, strengths, and thicknesses, followed by stamping to meet the needs of ensuring the overall accuracy of the parts and material heat treatment, improving the structural strength of the car body while reducing the overall weight. Aluminum alloy is widely used in the industrial field and is one of the essential light alloy materials for lightweight manufacturing in automotive manufacturing. This article discusses the splicing welding methods and processes of aluminum alloy sheets.
Arc welding is a traditional metal welding process of aluminum alloy, which has the advantages of mature technology and low cost. The arc welding processes applied to the splicing welding of aluminum alloy plates are mainly TIG tungsten arc welding and MIG welding (MIG welding) [5]. Aluminum alloy TIG welding is a common welding process (as shown in Figure 1), which uses tungsten electrode and parts as two electrodes, and inert gas (chlorine gas) as the protective gas to protect the arc. The process is relatively mature. MIG welding is the melting welding of welding wire. The welding heat melts the welding wire and the parts to be welded. The welding wire becomes a part of the final part, which is equivalent to the introduction of another kind of metal. It is easy to cause the problem of metal treatment. The welding is prone to crack, burn through, and the strength/hardness distribution ladder of the parts is large.
Figure 1 Tungsten chloride arc welding of aluminum alloy
Laser welding is a technology that uses high-energy laser as a welding heat source to melt and weld the metal in the welding area of a part (as shown in Figure 2). Although the energy density of laser welding is high, the total heat is small, the affected area is small, the weld seam is small, and the joint quality is good [6]. The laser welding process does not require gas protection, has low environmental requirements, fast welding speed, and high work efficiency. The welding characteristics of aluminum alloy and steel are quite different. When laser welding is applied to the welding process of aluminum alloy materials, several additional points need to be paid attention to, for example, aluminum alloy has a large coefficient of thermal expansion. In order to avoid excessive stress and deformation, preheating measures need to be taken; Laser welding has a fast cooling speed and is prone to generating hydrogen pores at aluminum alloy welds. Surface treatment is required before welding, and alloy strengthening elements are easily lost during the welding process, resulting in lower weld strength. Strength design should be taken into consideration.
Figure 2 Laser Tailored Welding of Aluminum Alloy
Friction stir welding (abbreviated as FSW) is a technology that uses the heat generated by friction and plastic deformation of material parts to weld parts. It was first proposed and applied to the welding of aluminum alloy, magnesium alloy and other material parts [7]. This technology achieves the welding effect by inserting a high-speed rotating stirring needle and moving it along the weld seam between the workpieces, stirring the materials softened by friction heat on both sides of the weld seam and fusing them (as shown in Figure 3). Friction stir welding is different from the traditional fusion welding technology. Its actual welding temperature is lower than the melting point of the base metal. Therefore, there is little change in the material structure at the weld joint, and the residual stress after welding is small. It is not easy to produce cracks, pores and other defects. The welding base material is the welding material, which does not introduce other metals, does not have metal treatment problems, and does not require welding wires, making the operation convenient.
Figure 3 friction stir welding
With the development of technology, advanced welding processes such as aluminum alloy laser arc composite welding and laser plasma arc composite welding have also emerged. This technology utilizes the combined effect of two heat sources, laser and arc or plasma arc, in the process of welding parts. By combining the advantages of the two processes, the quality of coal welding has been greatly improved. Composite welding not only retains the characteristics of fast heating and high efficiency of laser welding, but also makes use of the characteristics of arc welding that can effectively eliminate weld porosity, cracks and other defects.
3 Stamping performance of aluminum alloy sheet welded together
The stamping performance of sheet metal mainly refers to the ability of sheet metal to resist various defects during stamping, which is specifically reflected in the aspects of forming limit, crack, wrinkling, thinning, necking, springback and strength. For tailor welded blanks, it also includes weld displacement, thickness, strength distribution, etc. [8]. The factors that affect the stamping performance of sheet metal not only include the characteristics of the material itself, but also include various process parameters during the stamping process, such as the initial shape of the sheet metal, blank holding force, stamping speed, punching pressure, surface friction, lubricant selection, etc. If hot forming or warm forming is used, it also involves heating temperature, mold temperature, holding time, etc. In addition to the above factors, the stamping of tailor welded blanks also needs to consider the strain hardening index of the weld seam, thickness difference of the tailor welded blanks, material tensile strength ratio, weld seam position, welding process parameters, and so on.
According to different requirements of welding components, common weld forms include butt weld, end weld, plug weld groove weld, lap weld and fillet weld, etc. Due to the complex forming process of heating, melting, solidification and cooling of the workpiece during welding, the microstructure in the weld area changes and the weld moves, and the plastic, strength and other mechanical and chemical properties of the materials in the weld and welding heat affected area have changed significantly compared with the base metal, The corresponding molding performance has decreased. In view of the stamping performance of aluminum alloy tailor welded blanks, the focus is on the characteristics of the welding zone, that is, the weld seam and the Heat-affected zone, in the stamping process. At present, the main hot research directions include: testing and research of mechanical properties of TWBs, finite element analysis of TWBs forming process, determination of forming limit diagram of aluminum TWBs, forming characteristics of aluminum alloy plates with different strength thicknesses, deformation characteristics and failure forms of welds, forming movement rules of welds and Heat-affected zone, prediction and control of stamping springback. The main research methods are forming experiment testing Theoretical model establishment and finite element simulation. This article mainly analyzes the development and current status of aluminum alloy welding and stamping technology applied in the automotive industry. Therefore, the main object of analysis is the performance of aluminum alloy butt welds in their stamping process and related research progress.
Overall, the presence of welds reduces the formability of the sheet metal, and the wider the weld seam and its affected area, the greater the performance reduction. Regarding the forming limit diagram, which is important for the stamping forming performance of tailor welded blanks, there are currently two testing and representation methods in existing research due to the performance differences between the mother plate and the weld seam area. One is to use the composite law to treat the tailor welded blanks as a whole and provide the forming curve of the entire body through testing. This method has certain errors; The second method is to test the base metal and weld seam separately and provide corresponding forming limit diagrams. The study on the influence of thickness ratio of the base material on the formability of tailor welded blanks shows that the formability of tailor welded blanks decreases with the increase of thickness ratio. In response to the influence of the geometric shape of the weld seam on the formability of tailor-welded blanks, Lin Jianping et al. studied the ultimate bulging height under four different forming curves: broken lines, parabolas, Spline curves, and arcs. They concluded that broken line shaped welds are prone to stress concentration, with the lowest ultimate bulging height, while arc shaped welds and tailor-welded blanks have the highest ultimate bulging height, and the size of their arc radius is an important influencing factor. Research has shown that the direction of the weld seam and the offset distance between the weld seam and the maximum deformation position also have a significant impact on the forming performance. The farther the weld seam is from the deformation center, the smaller the difference between the overall forming and the base metal, that is, the smaller the impact of welding on the forming performance of the plate.
4 The Application of Tailored Welding Plate Stamping Technology in the Automotive Industry
The earliest manufacturer of tailor welded blanks in the automotive industry was Honda Motors in Japan, which first appeared in the 1960s in the form of using leftover materials to manufacture body inner panels. Ford Motors in the United States also applied laser welding technology for body steel plates as early as the 1970s. With the increasing demand for automotive safety and the need to reduce manufacturing costs, this technology gained widespread attention and widespread application in Germany in the 1980s. In 1985, Thyssen Steel in Germany successfully produced the first batch of tailor-welded blanks with a width exceeding 2m, which were successfully used in the manufacturing of Audi sedan soleplates. The tailor-welded technology gradually became commercialized and was widely applied in the automotive industry worldwide. Companies such as Luxembourg Arcelor, South Korea Posco, and Japan JFE also invested significant research and development efforts.
In 1985, Toyota Motor Corporation of Japan began using tailor-welded blanks, consuming approximately 3.6 million steel plates annually for the production of tailor-welded blanks. Since 1994, the three major automotive companies in the United States, General Motors, Ford, and Chrysler, have started to use tailor-welded blanks extensively. By 1995, the annual usage scale of welded blanks for BMW cars in Germany had reached 1 million pieces, and by 2000, the total usage of welded blanks in the entire European automotive industry had reached 50 million pieces [12]. By the beginning of this century, Pinxing technology had been widely used in the manufacturing of various components in automobiles, including body structural components, exterior panels, interior panels, A-pillars and B-pillars, door inner panels, longitudinal beams, floors, wheelhouses, inner tailgates, crossbeam bumpers, etc. At present, the annual usage of welded blanks worldwide has reached 150 million pieces, with 70% in Central Europe, 20% in the United States, and 10% in Japan.
Since the early 1990s, domestic automobile manufacturers have been tracking laser welding technology for automotive steel plates, gradually introducing welding plate stamping technology, purchasing imported welding plates for stamping forming, and gradually forming domestically produced stamping production lines after years of development. In 1999, Baosteel introduced a laser welding test device to further study the technology of laser welded blanks. At the end of 2000, the laser welded blanks successfully trial produced were used for the manufacturing of FAW Xiaohongqi base plates. In October 2002, the first professional commercial production line for laser welded blanks in China was officially put into use by Wuhan ThyssenKrupp Group Welded Blank Co., Ltd. In December 2004, FAW Baoyou Company, invested by Baosteel, FAW, and Sumitomo Corporation of Japan, was established. It imported laser welded plate lines, uncoiling and cutting lines, and uncoiling and cutting lines from Switzerland and officially put into production, with an annual production capacity of up to 1 million pieces. The main domestic suppliers of welded blanks include Shanghai Baosteel Arcelo Laser Coal Blending Co., Ltd. and Guangzhou Huadu Baojing Laser Welded Blank Co., Ltd. Currently, there are more than 20 laser welded production lines in China, with an annual output of about 25 million pieces, forming a considerable scale.
5 Conclusion
Tailored welded plate stamping technology is one of the important measures for lightweight automotive currently. The application of this technology can reduce vehicle weight, reduce costs, and reduce pollution. It is currently widely used in the production of the automotive industry. This article introduces the welding process involved in aluminum alloy welding stamping technology, analyzes the stamping performance, influencing factors, and existing research progress of aluminum alloy sheet welding blanks, and finally introduces the application status and future development prospects of welding blanks stamping technology in the automotive industry.
Article transferred from Aluminum Plus