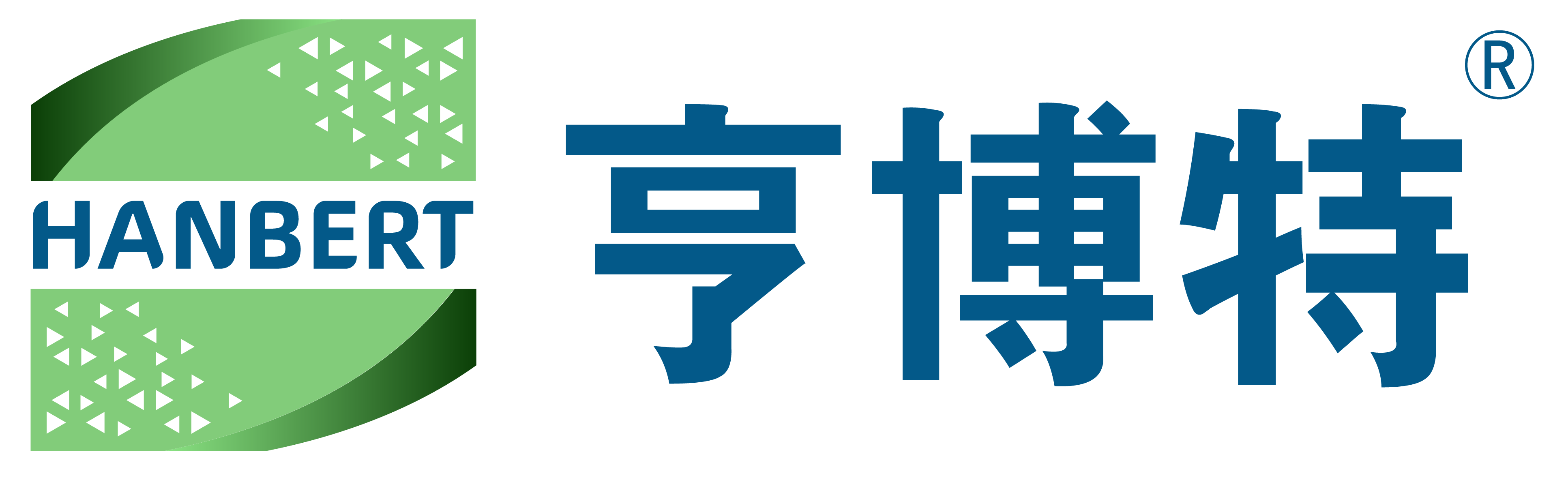
About anodizing
There are many metal surface treatment processes, such as powder spraying, electroplating, etching, polishing, wire drawing, sandblasting and anodizing. As the saying goes, the Great Wall is not built in a day. There are many processes and we need to learn them step by step. Today we mainly introduce anodization.
Anodizing is a very common and basic surface treatment process, which is widely used in the fields of aluminum alloy, titanium alloy and magnesium alloy.
The truth is that one connection leads to another, so this time we take the most commonly used aluminum alloy field as an example.
In short, aluminum anodizing can form a uniform and dense oxide film on the surface of aluminum products. Its chemical formula is Al2O3, commonly known as corundum. This name is well-known in the ore industry. Speaking of its family, there is a big brother and a big sister who are famous all over the world, that is, sapphire and ruby.
Of course, they are all naturally formed.
To get to the point, this oxide film has protective, decorative and other functional characteristics. From this definition, we need to correct a wrong understanding:
Many people think that aluminum oxide is to color aluminum. In fact, pure anodizing only involves the process of forming anodic oxide film. If it is necessary to color the metal, it needs to be dyed and sealed.
Anodizing type
General anodizing can make the surface hardness of the product reach 200-300hv; If it is a special product, it can be hard anodized, which can make the surface hardness of the product reach 400-1200hv, with good wear resistance. Therefore, hard anodizing is a necessary process in the aerospace field, and it is commonly used in transmission devices.
In ancient times, the building bucket arch was made of wood and transmitted the load. However, wooden bucket arches are flammable and easy to crack after long-term outdoor use. Modern building structures are mainly frame and shear wall structures, which do not need additional load-bearing functions. Therefore, wooden bucket arches have gradually ceased to be used, and antique architectural bucket arches have turned to durable, non combustible and light aluminum alloy bucket arches. The difference between anodizing and hard anodizing is that anodizing can be colored, and the decoration is much better than hard anodizing. Therefore, when someone mentioned hard anodizing in the future, it should be understood that this means hard anodizing, not general anodizing.
It is also necessary to mention another process - conductive oxidation, also known as chemical oxidation. It does not need to be electrified and is a pure chemical reaction, while anodizing needs to be carried out under high voltage, which is an electrochemical reaction.
The construction time of conductive oxidation is usually only tens of seconds, so the film is very thin, about 0.5-4 μ M (anodized film thickness: 5-30 μ m; Hard anodized film thickness: 25-150 μ m) Yes, but it can conduct electricity. It is generally used to help aluminum alloy prevent rusting and control resistance. It is often used in electrical components.
Process introduction
Common anodizing coloring process: general construction process is as follows: oil removal → alkali corrosion → chemical polishing → neutralization → Lidi → neutralization → anodization → dyeing → hole sealing → hot water washing → drying
The picture shows a large anodic oxidation tank
The picture shows the anodized parts suspended above the acid solution
The picture shows a small anodizing tank
Material requirements
Because the process is complex, the material requirements for anodizing are relatively strict, and different aluminum alloys will produce different decorative effects.
Commonly used are 6 series aluminum (60616063) and 7 series aluminum (7075) widely used in the mobile phone industry.
Because 2024 aluminum alloy contains more copper, it is easy to produce some gold spots during oxidation. 606160637075 does not have this problem.
It should be mentioned that die cast aluminum, such as A380, a365, a382, etc. According to the current production conditions, they can not be anodized. The reason is that in the production process of die-casting aluminum, in order to ensure the good fluidity of the aluminum liquid, some silicides need to be added. The anodized solution is usually acid, and the acid and silicon will produce a special reaction. It can be visually seen that the surface of the parts is blackened. This is also why most aluminum oxide parts are formed by CNC or extrusion. Divergent things may be biased toward engineering technology, but if designers want to transform CMF design, these knowledge also needs to be understood.
It is understood that at present, a certain manufacturer in the industry can realize the anodization of die-casting aluminum through the modification of die-casting aluminum. Of course, the cost is very high, which may be the precursor of the next reshuffle of the aluminum oxidation industry.
Collocation
What are the different effects of anodic oxidation combined with other processes?
Brushed fog surface natural color
Brushed bright face natural color
Brushed bright surface dyeing
Matte drawing dyeing
Sandblasting bright surface natural color
Sandblasting fog surface natural color
Sandblasting, dyeing, etc
Finally, talk about the future of anodic oxidation.
In recent years, the effect of anodic oxidation has been continuously improved, and a number of new anodic oxidation processes have been produced, such as two-color oxidation, gradual oxidation, micro arc oxidation and high polishing oxidation.
These new processes not only improve the surface effect, but also increase the cost. Finally, several photos of high-end oxidation objects are presented.
Porsche custom wheel hub (two color oxidation)
KEF MUO 2015 limited edition Bluetooth speaker (gradual oxidation)
Iphone7 bright black model (bright polished and oxidized)
Gear (micro arc oxidation MAO)
On the process of anodizing gradation treatment
The core of gradient color of anodizing is to dye the gradient color in the dyeing stage.
At present, there is a process of gradient color spraying, in which water-soluble ink containing dye is sprayed on the said anodic oxidation film layer, so that the thickness of the spraying liquid changes continuously. After coloring, it still needs to stand and wash before sealing the hole, but the effect is not very good.
The gradient anode method with better effect now is to control the coloring time in the coloring pool to realize the effect of gradient color. After anodic oxidation, a layer of oxide film is formed on the metal surface, and the dye enters the molecular gap of the oxide film during the dyeing process. The longer the dyeing time, the more dye enters, and the deeper the color. By controlling the time that the part to be dyed stays in the dye through the computer, for example, gradually pulling the workpiece away from the dye, a uniform gradation effect can be achieved. After sealing the hole, it is the so-called gradient anode process.
Of course, these are only a few methods. There are many methods for gradient color after anode, such as silver salt dyeing, pattern dyeing and thermal transfer printing. Because the mechanism of anode dyeing has been clearly studied, many dyeing processes have gradually developed methods that can be used for anode dyeing.
This is also the reason why basic theoretical research can promote the development of existing processes.