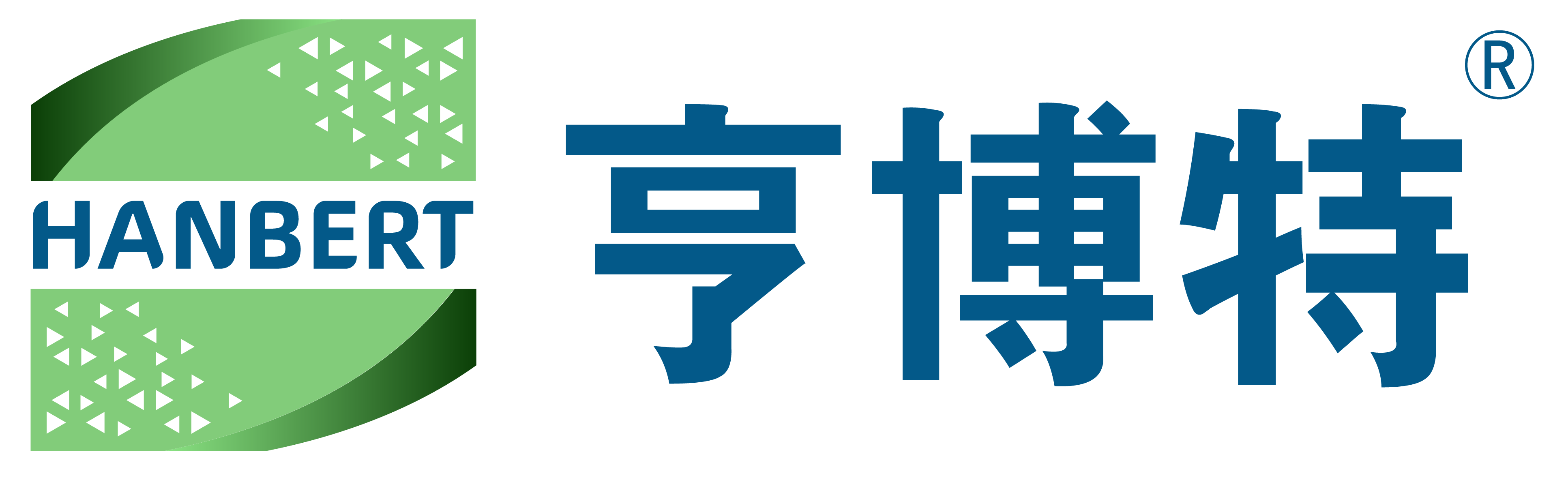
· Etching printing process
The etching printing process is to print a layer of uneven translucent ink on the substrate with smooth surface such as gold and silver cardboard, and then conduct light curing through a special ultraviolet lamp (UV) light source to produce an artistic effect similar to the etching or sanding treatment of the metal surface. Etching printing is one of the latest printing technologies in the world. Etched printed matter has infinite charm, giving people a sense of strangeness, freshness, three-dimensional feeling and artistic quality. The biggest feature of etched printing is that after printing, it will not cover the body color of the substrate, which has exquisite and transparent appreciation value.
· Lithography process
n the lithography process, because the graphic part and the non graphic part of the lithography are on the same plane, in order to make the ink distinguish the pattern part or the non pattern part of the printing plate, using the principle of oil-water separation, the water supply device of the printing plate components first supplies water to the non graphic part of the printing plate, so as to protect the non graphic part of the printing plate from being soaked by the ink. Then, the ink is supplied to the printing plate by the ink supply device of the printing part. Since the non graphic part of the printing plate is protected by water, the ink can only be supplied to the graphic part of the printing plate. Finally, the ink on the printing plate is transferred to the milk skin, and then the ink on the milk skin is transferred to the substrate by using the pressure between the rubber roller and the embossing cylinder to complete one printing; So. Lithography is an indirect printing method.
· Hot stamping
Lettering, hot stamping, commonly known as "bronzing", has a long history in China. It refers to the words and patterns of materials such as colored foil on the first or fourth seal of the hardcover book cover and the back of the book, or various concave and convex book titles or patterns printed by hot pressing.
· Color Pattern Coating
Water transfer technology is a kind of printing that uses water pressure to hydrolyze the transfer paper / plastic film with color pattern. The technological process includes the production of water transfer paper, soaking, pattern transfer, drying and finished products.
· IMD
IMD, i.e. in mold decoration technology, can be IMR, IML and IMF according to its production mode. IMR (in mold roller): in mold ink transfer is an in mold decoration technology that transfers the ink attached to the film to the product appearance through injection molding, and then reveals the film through the mold opening process. Ml (in mold labeling): placement labeling is to place the appearance label cut by the printed matter into the mold by manual or manipulator, and then attach it to the appearance surface of the finished product by injection molding.
· Etch
Etching is the technology of removing materials by chemical reaction or physical impact. Etching technology can be divided into wet etching and dry etching. Generally, the etching is also called photochemical etching, which refers to removing the protective film of the area to be etched after plate making and development by exposure, and contacting the chemical solution during etching to dissolve the corrosion and form the effect of concave convex or hollow forming.
· 3D diamond carving
3D diamond carving refers to the trace left by the rotation of the diamond tool on the metal surface. This process can be applied not only in the finishing field of general products, but also in mold manufacturing.
· Electrophoretic coating technology
Electrophoretic coating technology is a coating method that uses an external electric field to make the particles such as pigment and resin in suspension and electrophoretic solution migrate and deposit on the substrate surface of one of the motors. Electrophoretic coating is a special film forming method developed in recent 30 years.
· Powder coating
Powder coating uses the function of high-voltage electrode. When passing through this ion cloud, powder particles absorb negative ions and are negatively charged. Powder coating can reduce environmental pollution, effectively reduce costs and improve production capacity.
· Optical coating technology
Optical coating technology refers to the process of coating a layer (or multiple layers) of metal (or medium) film on the surface of optical parts. The purpose is to reduce or increase the reflection, beam splitting, color separation, filter, polarization and other requirements of light. The common method is to coat thin films on glass substrates by means of vacuum sputtering.
· Embossing process
The embossing depth of the working roll is 0.03mm-0.03mm, which can be eroded on the metal plate due to different rolling process. Aluminum embossing is calendering and other processing on the basis of aluminum plate. Thus, various patterns are formed on the surface of the aluminum plate. Embossed aluminum plate is mainly used in packaging. Integrated ceiling, building curtain wall, etc.
· Surface hardening technology
Surface hardening technology refers to hardening the surface layer of parts through appropriate methods, while the core of parts still has strong and tough treatment. PMMA is an organic material with low hardness and is more prone to scratches. Therefore, the surface must be hardened. This process is called PMMA acrylic surface hardening. This kind of panel is often used on various display panels that are often touched, such as mobile phones, display screens, instrument panels and so on. Because the acrylic plate without hardening is not scratch resistant, the hardness of the acrylic plate treated by surface hardening can be increased from h to more than 4H.
· Galvanized
Galvanizing refers to the surface treatment technology of plating a layer of zinc on the surface of metal, alloy or other materials to play the role of beauty and rust prevention.
· Powder spraying
Powder spraying is to spray powder coating onto the surface of the workpiece with powder spraying equipment (electrostatic plastic spraying machine). Under the action of static electricity, the powder will be evenly adsorbed on the surface of the workpiece to form a powdery coating; After high temperature baking, leveling and curing, the powder coating becomes the final coating with different effects (different kinds of effects of powder coating).
· Micro arc oxidation
Micro arc oxidation (MAO), also known as micro plasma oxidation (MPO), is the growth of ceramic films dominated by matrix metal oxides on the surfaces of aluminum, magnesium, titanium and their alloys by the action of instantaneous high temperature and high pressure generated by arc discharge through the combination of electrolyte and corresponding electrical parameters.
· Metal wire-drawing
Metal wire drawing is a manufacturing process of repeatedly scraping aluminum plates out of lines with sandpaper. Its main process is divided into three parts: degreasing, sanding mill and water washing. In the wire drawing process, the special film technology after anodic treatment can make the metal surface generate a film layer containing the metal component, and clearly show each fine wire mark, so as to make the metal matte with fine hair luster.
· Enameling
Blue burning is to fill the whole carcass with colored glaze and then bake it in a blast furnace with a furnace temperature of about 800 ℃. The colored glaze melts from sand like solid into liquid and becomes a gorgeous colored glaze fixed on the carcass after cooling. At this time, the colored glaze is lower than the height of copper wire, so it has to be filled with colored glaze again, and then sintered for four or five consecutive times, until the pattern is filled to the level of wire pinching pattern.
· Frosting
Sanding is a process that makes the object with smooth surface become unsmooth and makes light shine on the surface to form a diffuse reflection. In chemical sanding treatment, the glass is mechanically or manually ground with emery, silica sand, pomegranate powder and other abrasives to make a uniform and rough surface. The surface of glass and other objects can also be processed with hydrofluoric acid solution, and the resulting product becomes frosted glass.
· TTO
Heat transfer printing is a new printing technology introduced from abroad. The printing method of thermal transfer process is divided into two parts: transfer film printing and transfer processing. The transfer film printing adopts dot printing (resolution up to 300dpi), and the patterns are pre printed on the film surface. The printed patterns are rich in layers and bright colors. It has the advantages of ever-changing, small color difference and good reproducibility, which can meet the required effect of the designer, and is suitable for mass production.
· Radium carving
Laser engraving, also known as laser engraving or laser marking, is a surface treatment process based on optical principles. Use a laser beam to carve a permanent mark on the surface of a material or inside a transparent material. Laser beam can produce chemical effect and special effect on matter. When a substance instantly absorbs laser light, it produces a physical or chemical reaction, so as to engrave marks or show patterns or words.。
· PVD
PVD is the abbreviation of physical vapor deposition in English. It refers to that under vacuum conditions, using low-voltage and high current arc discharge technology, using gas discharge to evaporate the target and ionize the evaporated material and gas, and using the acceleration of electric field to deposit the evaporated material and its reaction products on the workpiece. The films prepared after PVD have the advantages of high hardness, low friction coefficient, good wear resistance and chemical stability.
·Electroplate
Electroplating is a process of plating a thin layer of other metals or alloys on some metal surfaces by using the principle of electrolysis. It is a process of using electrolysis to attach a metal film to the surface of metal or other material parts, so as to prevent metal oxidation (such as corrosion), improve wear resistance, conductivity, reflection, corrosion resistance (copper sulfate, etc.) and enhance beauty. The outer layer of many coins is also electroplated.
· Calendering
Calendering is also called calendering. The last process of re leather finishing. Using the plasticity of fibers under mixed heat conditions, the fabric surface is flattened or rolled into parallel fine oblique lines to improve the finishing process of fabric luster. After the material is fed, it is heated and melted, then formed into a sheet or film, and then cooled and rolled up. The most commonly used calendering material is polyethylene.
· Flat screen printing
Flat screen printing, the printing die is a polyester or cotton fiber or cotton fiber screen (pattern) fixed on the square frame and with hollow pattern. The pattern on the pattern plate can pass through the color paste, and the mesh without pattern is closed with polymer film. During printing, the pattern plate presses the fabric tightly, and the pattern plate holds the color paste, which is scraped and pressed back and forth with a scraper to make the color paste reach the fabric surface through the pattern. Flat screen printing has low production efficiency, but it has wide adaptability and flexible application. It is suitable for small batch and multi variety production.
· Spray
Spraying is a coating method that disperses into uniform and fine droplets through a spray gun or disc atomizer with the help of pressure or centrifugal force and is applied to the surface of the coated object. It can be divided into air spraying, airless spraying, electrostatic spraying and various derived methods of the above basic spraying forms, such as high flow low-pressure atomization spraying, thermal spraying, automatic spraying, multi-group spraying, etc.
· Spraying technology - PU paint
PU paint is sprayed by spray gun or TV atomizer, which is dispersed into uniform and fine droplets by means of pressure or centrifugal force and applied to the surface of the coated object. PU paint is the general name of all polyurethane coatings. Its film-forming method is natural film-forming without special process. PU paint spraying is to spray a layer of PU paint on the surface of the workpiece.
· PET film UV transfer
PET film UV transfer uses the non stick characteristics of UV transfer glue and metal to transfer the ultra-thin key effect of various mobile phones to PET sheet through UV transfer process, so as to make ultra-thin keys and key type including CD pattern, vertical drawing, fog surface, bright surface pattern and other effects.
· Laser biting
Laser flower biting uses high-energy density laser to react with the steel surface to form snake skin / etched lines / pear ground or other forms of lines. Make the product more beautiful and elegant: overcome the shortcomings of printing and painting that are easy to wear off; It meets the visual requirements: because the surface of the product as smooth as a mirror is easy to be scratched, stained with dust and fingerprints, and the defects, silk marks and ripples generated in the formation process will be exposed on the smooth surface of the product, while some decorative patterns such as leather grain, orange peel grain, wood grain, rain flower grain and matte surface can hide the defects of the product surface in the forming process, so as to make the product beautiful and meet the visual needs.
· Sandblasting
Sand blasting uses compressed air as power to form a high-speed jet beam to spray materials (copper ore, quartz sand, carborundum, iron sand and Hainan sand) to the workpiece surface to be treated at high speed, so as to change the appearance or shape of the outer surface of the workpiece surface. Due to the impact and cutting effect of abrasive on the workpiece surface, the workpiece surface can obtain certain cleanliness and different roughness, and the mechanical properties of the workpiece surface can be improved, Therefore, it improves the fatigue resistance of the workpiece, increases the adhesion between it and the coating, prolongs the durability of the coating film, and is also conducive to the leveling and decoration of the coating.
· EDM
Electrical discharge machining (EDM) is a special machining method that uses the electric erosion produced by the pulse discharge between the two poles immersed in the working fluid to etch away the conductive materials. It is also known as electrical discharge machining or electric erosion machining, which is called EDM for short. Tool electrodes are often made of corrosion-resistant materials with good conductivity, high melting point and easy processing, such as copper, graphite, copper tungsten alloy and molybdenum. In the process of machining, the tool electrode also has loss, but it is less than the corrosion amount of workpiece metal, and even close to no loss.