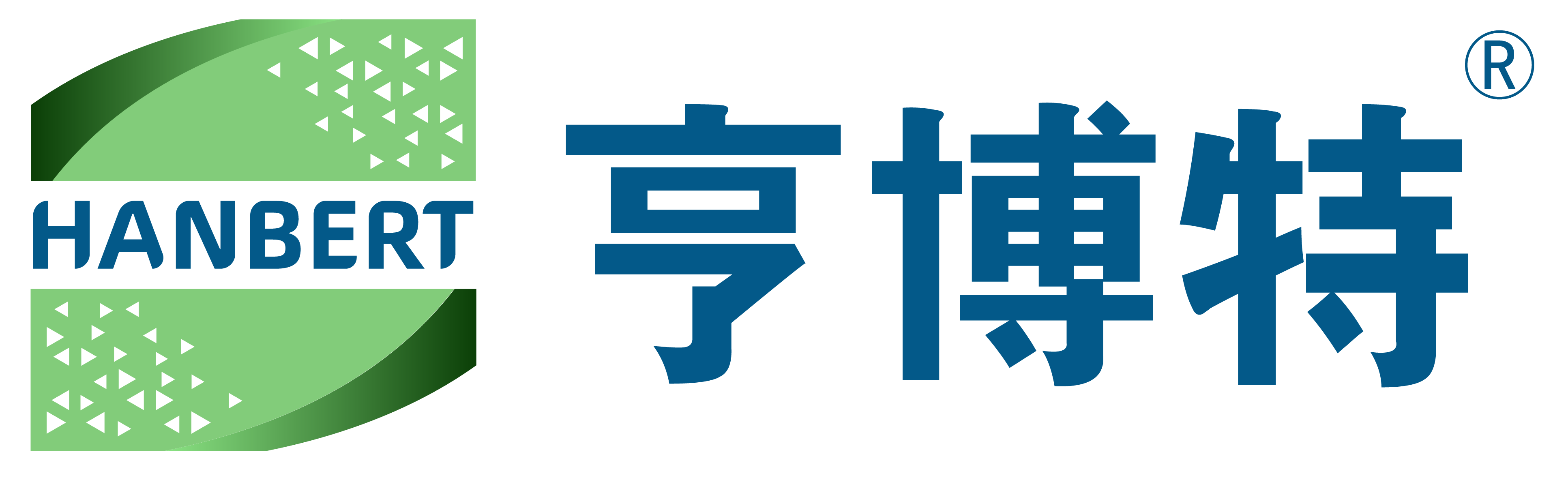
1、 Aluminum composite panel curtain wall system
(1)Structure
Dragon bone: steel profile; Vertical frame 3x50mmx100mm square tube, horizontal frame 50X5m equilateral angle steel; Galvanized anti-corrosion treatment.
(2)Materials
The surface material is made of 4mm fluorocarbon sprayed aluminum composite panels, with aluminum alloy reinforcement bars uniformly distributed at a spacing of 500mm along the long side direction. The insulation is 50mm fireproof insulation rock wool, and the interlayer fireproof is supported by 1.5mm galvanized steel plates and 100mm thick fireproof rock wool. Indoor and outdoor visible carbon steel components are treated with fluorocarbon spraying, while the rest are hot-dip galvanized. The connecting bolts and screws are made of stainless steel material, with 316 for the outdoor part and 304 for the indoor part; Indoor and outdoor visual connection bolts are decorative bolts.
2、Construction sequence
During construction, zoning and layered installation should be followed; Install the skeleton first and then the decorative panel; First overall, then local; The construction principle of first covering the surface and then closing the mouth. In order to ensure the orderly progress of the overall project according to the plan, it is necessary to fully prepare for each construction stage, process, aspect, and link, so that the construction space of the overall project is fully occupied, and the time is balanced, continuous, and rhythmic.
During the construction process of the main structure, the installation of embedded parts and measurement and laying out should be interspersed. The construction sequence is from bottom to top.
Firstly, number the facade components of the curtain wall, and according to the construction schedule of the construction site, issue a corresponding component processing notice to the processing plant in advance to organize processing. The processing plant organizes production and processing, and after the finished product is inspected and qualified, a product certificate should be issued, and the product should be numbered and registered for protection. According to the site requirements, transport it to the construction site for hoisting to reduce the requirements of the construction site for the site area and minimize the impact of cross operation on other construction units. The reference point for curtain wall installation is the connecting piece between the curtain wall and the main body. Therefore, when measuring and setting out, the centerline of the connecting piece should be determined and used as the reference for curtain wall installation.
After being processed and formed in the factory, aluminum composite panels are transported to the site for direct installation. The installation of aluminum-plastic panels for curtain walls should be carried out in sequence from bottom to top.
3、Construction plan for hidden frame aluminum-plastic panel curtain wall
3.1 Construction Preparation
Before the construction of aluminum-plastic panel curtain wall, the specifications of the required materials and the quantity of various accessories should be accurately provided according to the design requirements for processing.
(2)Before construction, compare the skeleton design of the aluminum-plastic panel curtain wall and recheck the quality of the main structure. The quality of the main structure has a significant impact on the arrangement position of the curtain wall skeleton. Especially the deviation of wall verticality and flatness will affect the horizontal position of the entire curtain wall.
(3)Thoroughly verify the construction drawings and on-site measured dimensions to ensure the completeness of the design and processing.
(4)Main machinery and equipment
①Mechanical equipment
Impact drill, grinding wheel cutting machine, welding machine, rivet gun, electric screwdriver.
②Main equipment
Screwdriver, pliers, wrench, plumb bob, spirit level, steel tape measure.
3.2 Homework conditions
(1)The main structure has been constructed. The main construction has already embedded the pre embedded parts according to the design requirements.
(2)Set up a separate warehouse on site to prevent damage to incoming materials. After entering the warehouse, components should be stacked on wooden pads according to their type and specifications. Before installation, all components should be inspected and calibrated. The components should be straight, square, and free from deformation and scratches. Unqualified components shall not be installed.
3)The aluminum-plastic panel curtain wall relies on scaffolding for construction. Before installation, the aluminum-plastic panel and accessories are transported to each construction surface layer by stairs according to the height and width specified in the curtain wall skeleton design drawings.
3.3 Measurement and laying out
(1)Print out all pre embedded items and retest their position dimensions.
(2)Determine the social width and access dimensions of the wall at the bottom level based on the baseline.
(3)Use a theodolite to draw several vertical lines upwards to determine the corner position and facade dimensions of the curtain wall.
(4)Determine the centerline of a facade based on the axis and centerline.
(5)When measuring and setting out, the allocation of errors should be controlled to prevent error accumulation.
(6)The measurement and laying out shall be carried out under wind conditions not exceeding level 4. After laying out, it should be checked in a timely manner to ensure the verticality of the curtain wall and the correctness of the position of the columns.
3.4 Skeleton Installation
3.4.1Fixed skeleton connectors
The crossbeam and vertical frame plates of the skeleton are fixed to the main structure through connectors, and the connectors can be welded to the embedded parts of the main structure. The verticality of the columns can be controlled by a plumb bob, and only after accurate position adjustment can the iron code be officially welded to the embedded iron parts. Installation error requirements: elevation soil 3m; front and rear soil 2mm; left and right soil 3mm. Expansion bolts can also be installed on the walls of the main structure. Because the latter method is more flexible, with small dimensional errors, and easy to ensure the accuracy of quality, it is more commonly used. Steel type connectors should be galvanized on the surface and rust proof paint should be applied to the welds.
3.4.2 Column installation
The steel columns of this aluminum composite panel curtain wall are made of galvanized steel pipes.
Columns are generally vertical components and are one of the key components in the installation and construction of curtain walls. Its accuracy and quality will affect the installation quality of the entire curtain wall. The allowable deviation between the plane axis of the connecting curtain wall and the outer plane axis of the building should be controlled within 2mm, especially for curtain walls with curved, circular, and enclosed building planes. The distance between the inner and outer axes will affect the circumference of the curtain wall and should be taken seriously.
The steel column adopts the sleeve connection method. If the connection between the connecting piece and the embedded part is a two-story building or a whole piece, in order to enhance the stiffness of the curtain wall frame, the connection points between the columns and the main structure can be appropriately increased. Adopting a spaced hinge and rigid connection structure, the hinge only resists horizontal forces. When the connection point is in brick masonry, expansion bolts cannot be used for the connection, and through wall bolts should be used for fixation; In addition to resisting horizontal forces, it should also bear vertical forces and transmit them to the main structure.
3.4.3Installation of crossbeam
The steel crossbeam of this aluminum-plastic panel curtain wall is made of galvanized angle steel. The crossbeam is generally a horizontal component, which is embedded and connected in sections in the column. The connectors at both ends of the crossbeam are installed at the predetermined positions of the column. The crossbeam should be placed on the connecting piece without being fixed, and the cutting length should be intentionally slightly shortened during production to create a certain gap at the joint. Due to the sleeve connection between the columns, there is a gap at the joint, and there is also a gap between the crossbeam and the columns, so that the columns and crossbeams can form a frame skeleton with certain deformation ability after installation, to adapt to and eliminate the influence of building deflection deformation and temperature deformation, and improve its bearing capacity. But if the crossbeam has arcs, folds or corners, to prevent it from falling off, the crossbeam should be fixed to the connecting piece.
Installation accuracy of crossbeams: The horizontal elevation deviation of adjacent crossbeams should not exceed 1m, the elevation deviation of the same floor should not exceed 4mm, and the height deviation from the column surface should not exceed 1mm. The installation of crossbeams on the same floor should be carried out from bottom to top. After installing a layer of height, it should be inspected, adjusted, calibrated, and fixed to meet quality requirements. The elevation difference of horizontal beams on the same floor should not exceed 5mm (width below 35m) and 7mm (width above 35m). Section, with a maximum adjustment length of 30mm (i.e. the secondary keel can be adjusted up and down), and then connect the secondary keel to the dedicated bracket with bolts.
3.5Installation of lightning protection system
The edge closure of aluminum-plastic panel curtain wall is a vulnerable area to lightning strikes, especially at the corners where the lightning strike rate is highest. For this purpose, on the one hand, the company directly uses building lightning rods; On the other hand, the edge sealed aluminum plate is used as a lightning arrester, which is connected to the steel bars inside the structural parapet wall to form an electrical circuit, and the negative current to the ground is not greater than 42.
3.6Anti corrosion treatment
The keel of the aluminum-plastic panel curtain wall in this project is made of steel, and its anti-corrosion is extremely important. Although the steel keel of its curtain wall is hot-dip galvanized, the galvanized layer is damaged during processing and installation, so secondary anti-corrosion treatment must be carried out on the keel (the damaged part of the galvanized layer). The secondary anti-corrosion treatment adopts two coats of epoxy zinc rich paint. After painting, it is necessary to carefully inspect and keep records.
3.7 Treatment of the Closing Area
3.7.1Inner and outer corner treatment
(1)Treatment of interior wall corners
At the corner of the aluminum panel curtain wall, a vertical frame is usually erected at the corner, and two aluminum panels are fixed to the sub frame at the intersection. The sub frame is overlapped and fixed on the solid frame.
2)External corner treatment
At the corner, use specially designed single-layer aluminum plates to overlap with the aluminum plates at both ends and fix them to the horizontal frame.
3.7.2Window processing
Fix the specially made aluminum profile with the window corner profile, seal the joint with the aluminum plate with sealant.
3.7.3Treatment of upper parts
(1)Aluminum panels and sub frames form a top cover, enclosing the parapet wall. The sub frame, horizontal frame, and parapet are fixed with corner aluminum. Seal the seams.
(2)Top pressing treatment
The so-called top pressing treatment refers to fixing aluminum alloy plates on both sides of the parapet wall, and using waterproof materials at the joints.
3.7.4Treatment of lower parts
There are two ways to treat the lower part of the aluminum composite panel curtain wall
(1) Supported on the corner code
When installing the lower end of the aluminum plastic panel curtain wall, the frame and aluminum panel cannot directly contact the ground, nor can they be directly inserted into the soil, but are supported on the corner code, which is sealed with foam strips and weather proofing glue.
(2)Set up slope water board closure
The lower part of the aluminum composite panel curtain wall is sealed with a specially designed sloping water board, which also covers the gap between the board and the wall to prevent rainwater from seeping into the room from this area. The slope board and the ground are sealed with foam strips.
3.7.5Closing treatment of wall edges
At the edge of the curtain wall, aluminum plates formed from aluminum alloy are used to seal the end of the curtain wall and the keel, and waterproof materials are used for sealing.
3.7.6Treatment of Expansion and Settlement Joints
The treatment of expansion joints and settlement joints should first consider adapting to the needs of building expansion and settlement. This part is also a weak link in waterproofing. Usually, neoprene is used to make expansion joints. The joint edges are filled with polyethylene foam, and the outer edges are sealed with glue.
3.8Weather resistant adhesive joint filling
When applying weather resistant sealant to joints, attention should be paid to:
(1)Clean the gaps between the boards without water, oil stains, paint, rust, cement mortar, dust, etc. The bonding surface should be thoroughly cleaned and dried. Toluene or methyl diethyl ketone can be used as cleaning agents.
(2)To adjust the depth of the seam and avoid adhesive on three sides, polyethylene foam material (small round rod) should be filled inside the seam.
(3)To avoid contaminating glass and aluminum plates with sealant, protective tape should be applied on both sides of the seam.
(4)After gluing, the surface of the glue joint should be smoothed and excess glue should be removed.
(5)After the glue injection is completed, tear off the protective tape and wipe it with solvent if necessary.
(6)After the adhesive is fully hardened, do not let it get dirty or scratched.
(7)The depth (thickness) of the joint sealant should be less than the width of the joint, because when the board undergoes relative displacement, the adhesive is stretched. The thicker the gap, the greater the stretching deformation of the edge, and the more likely it is to crack.
(8)Weather resistant silicone sealant should form a double-sided bond inside the joint, not a three sided bond, otherwise the adhesive is prone to tearing under tension and will lose its sealing and anti leakage function. To prevent the formation of three sided bonding, before applying weather resistant silicone sealant, lay non adhesive tape at the bottom of the gap and separate the bottom of the gap from the adhesive.
4、Quality standard