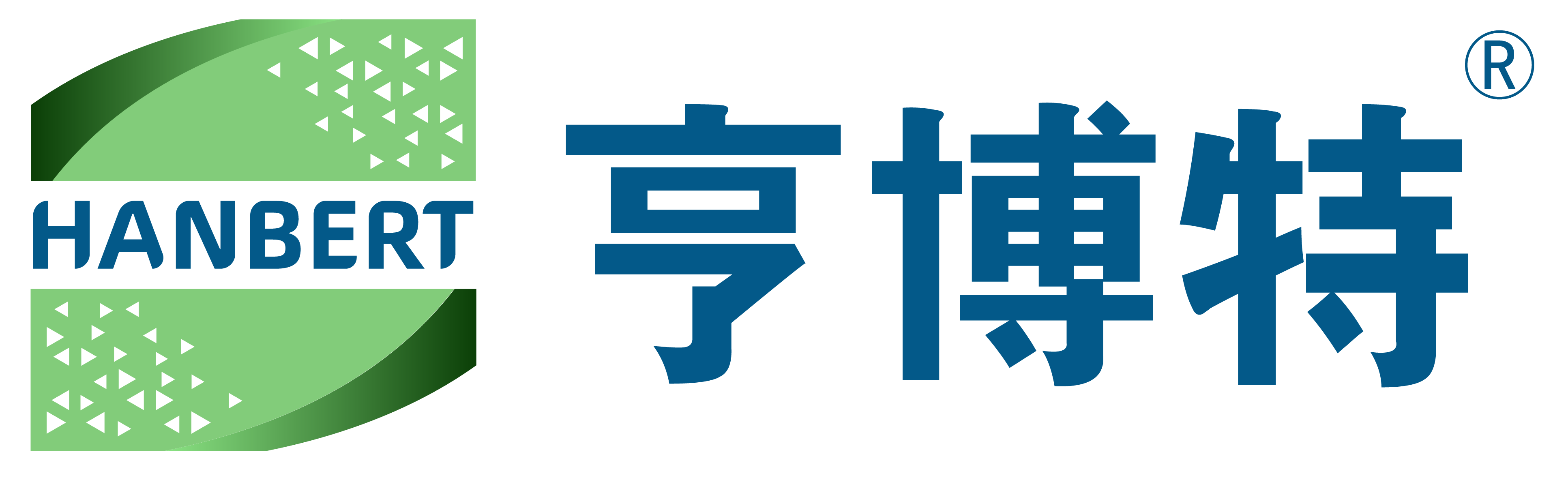
Abstract: Aluminum plate tomb walls, as a commonly used material for modern building facades, have a direct impact on the overall aesthetics and construction quality of the building's appearance due to their flatness. This article analyzes various reasons for the insufficient flatness of aluminum panel curtain walls (as shown in Figures 1 and 2), including deviation in aluminum panel processing accuracy, non-standard installation processes, errors in keel installation, material deformation, and environmental factors. Through a systematic analysis of these reasons, targeted solutions are proposed, such as optimizing the design and processing technology of aluminum panels, strengthening quality control during installation, adopting high-precision keel installation technology, and reasonably controlling material storage and construction environment. The use of these measures can significantly improve the flatness of aluminum panel walls, enhance the quality and durability of buildings and facades, and provide scientific basis and practical guidance for the design, construction, and maintenance of aluminum panel tomb walls.
Figure 1 Flatness Defect of Aluminum Curtain Wall on Building Facade
Figure 2 Flatness Defect of Aluminum Curtain Wall on Building Facade
ONE、Analysis and Solutions for Insufficient Flatness of Aluminum Curtain Wall
1、The division of the building facade is unreasonable, and the aluminum plate specifications are too large
Reason analysis: Architects pursue large-scale facade division mainly to achieve a simple and atmospheric visual effect, enhance the overall sense and high-end quality of the building. Some architects, due to various reasons, lack confidence in the material of the facade and choose aluminum panels as enclosure materials. However, the aluminum panel material determines that it cannot resist the defect of insufficient flatness in large-sized situations, which in turn affects the overall effect of the building facade.
Solution: Negotiate with the architect to adjust the grid size, which should not be too large; Aluminum plates should be used with caution in special locations, and materials such as honeycomb aluminum plates or high-quality composite aluminum plates should be considered to better address the issue of insufficient flatness. Particularly recommended are honeycomb composite plates with diffuse reflection or frosted surfaces.
Extended analysis: ① Advantages of aluminum honeycomb panel: good flatness, for projects with high requirements for external facades, aluminum honeycomb panel is the best choice; At the same time, it can achieve a super large size of 1.5 * 4.5 meters while maintaining high flatness; The disadvantage is that the cost is slightly higher, more than 20% more expensive than ordinary aluminum veneer; Aluminum honeycomb panels can be bent and curved, but they cannot have the same flatness and surface treatment effect as aluminum or aluminum-plastic panels, which are increasingly used in high-end curtain wall projects. They have high plasticity and are difficult to create complex shapes High end imported A-grade fireproof aluminum-plastic panels can also be used for building facades, but their prices are expensive. The world's first aluminum composite panel was named ALUCOBOND (Figure 3), and the most famous imported aluminum composite panel brand today is Aruk Bang in Germany, but the disadvantage is that it is very expensive.
Figure 3 ALUCOBOND7m ultra long and ultra flat aluminum composite panel curtain wall effect
2、Wrong selection of aluminum plate material
Reason analysis: The material used for the aluminum curtain wall on the exterior facade of the building is 1 * * series aluminum panels. Aluminum curtain walls should not use 1 * * series aluminum panels, mainly because of their low strength and inability to be strengthened through heat treatment. 1 * * * series aluminum plates belong to industrial pure aluminum, with relatively low tensile strength and hardness, making it difficult to meet the strength requirements of aluminum curtain walls under wind loads, self weight and other factors. In addition, the machinability of 1-series aluminum plates is poor, difficult to brazing, prone to deformation under pressure, and prone to deformation during wall processing and installation, which affects the overall flatness and stability.
Solution: According to the "Technical Code for Metal and Stone Curtain Wall Engineering" JGJ133-2001, aluminum veneers for building curtain walls should preferably be made of alloy aluminum materials such as the 5 * * * series of tall and large yuan, with states H14 (slightly higher strength) and H24 (commonly used), and tensile strength generally above 120. The 1 * * * series (pure aluminum, soft quality) should never be used.
3、Considering only economy, the selection of aluminum plate thickness is incorrect
Reason analysis: The project considers economy and optimizes the thickness of the aluminum plate. Although the standard requires a minimum thickness of 2.5mm for aluminum veneers (2.5 and 3.0mm are more commonly used in actual engineering), it may not be a problem for some small grid positions. However, when the size of the aluminum plate is large, it often leads to insufficient flatness of the aluminum plate.
Solution: Increase the thickness of the aluminum plate. The revised JGJ133 standard has added a method of determining the minimum thickness of the substrate using the strength of the aluminum plate. Generally, when the yield strength of the aluminum plate is less than 100mpa, the thickness is greater than 3.0mm. When the strength of the aluminum plate is between 100 and 150, the thickness is greater than 2.5mm. When the strength of the aluminum plate is greater than 150, the thickness is greater than 2.0mm.
It should be noted that although different grades of aluminum plates have different strengths, their elastic modulus E is the same. Therefore, when using high-strength alloy aluminum plates with smaller plate thickness, ribs should be densified to reduce the spacing between strengthening ribs, in order to ensure the rigidity and surface flatness of the panel.
4、The design of aluminum plate stiffeners is not clear
Reason analysis: The metal plate is relatively thin, and if necessary, reinforcement ribs should be installed to increase its stiffness and maintain the flatness of the plate surface, as shown in Figure 5. If the design of the aluminum plate surface does not specify whether to arrange stiffeners or specific configuration requirements, it may lead to the manufacturer configuring stiffeners according to the minimum requirements or simply not configuring stiffeners. In addition, the stiffeners are not connected to the folded edges, and the rib direction is arranged incorrectly (along the short edge), which may also lead to their failure, especially for some large-sized aluminum plates, resulting in poor stiffness and flatness.
Figure 4: Aluminum plate arrangement with stiffeners
Strengthening ribs are the supports for aluminum plates when subjected to surface loads. Strengthening ribs become locations with relatively large deformations and should be reliably connected to the panel. The middle ribs that serve as supporting edges in metal plates should be reliably connected to the edge ribs or the folded edges of single-layer aluminum plates. The connection between the middle ribs supporting the metal panel grid and their intersecting middle ribs should meet the requirements of force transmission.
Figure 5: The reinforcing ribs of the aluminum plate should be effectively connected to the folded edges
As the supporting edge of the panel, the reinforcing ribs are the immovable supports of the panel grid, so the reliable connection between the middle ribs and the edge ribs (Figure 5), as well as between the middle ribs, should be ensured to meet the force transmission requirements. In some engineering projects, the middle rib is only considered to ensure the flatness of the panel and is not used as the supporting edge of the panel. In this case, the middle rib is only connected to the panel and is not connected to the edge rib or the edge of the single-layer aluminum plate. The middle rib is in a floating state without support and cannot be used as the supporting edge of the grid panel. At this time, the supporting edge of the middle rib should not be considered when calculating the panel.
Solution: Aluminum plates have limitations in the width direction. Conventional plates with a width of less than 1200mm can be made, while plates with a width of less than 1500mm can be made. However, plates with a width exceeding 1500mm are called ultra wide plates, and there are no limitations in the length direction. Especially for some ultra wide plates, the calculation of aluminum plate stiffeners should be determined through structural calculations and strictly processed and arranged according to the design. It is recommended that aluminum plate stiffeners should be selected with larger profile sections, materials (steel ribs) or densely arranged, and attention should be paid to the arrangement direction (along the long side).
5、Aluminum plate not folded or folded with insufficient height
Reason analysis: Aluminum sheet folding is sent to the aluminum sheet factory for material quotation. Generally, there is no separate charge for materials within 20mm, and the cost will be calculated based on the unfolded area for the excess part. Therefore, some projects consider economy, resulting in the aluminum sheet not being folded or the height of the folded edge being insufficient, which will weaken its edge strength and cannot effectively resist external forces, making it more prone to deformation during installation, transportation or use, affecting the overall flatness. At the same time, insufficient folding can also reduce the stability of the connection between the aluminum plate and the keel, increase installation errors, further exacerbate flatness problems, and be more prone to wavy deformation due to thermal expansion and contraction during temperature changes, ultimately affecting the overall quality and visual effect of the aluminum plate curtain wall.
Solution: Increasing the folding height of the aluminum plate and combining it with a high stiffness frame can effectively form a structure similar to a prestressed plate, thereby significantly improving the flatness and overall performance of the aluminum plate. The increase in the height of the folded edge can form a "" shaped load-bearing structure, enhancing the rigidity of the aluminum plate. At the same time, the high stiffness frame can further constrain the deformation of the aluminum plate, and through the effect of prestressing, the aluminum plate can maintain better flatness and stability after installation. This design not only improves the deformation resistance of the aluminum plate, but also effectively responds to temperature changes and external forces, reducing deformation caused by factors such as thermal expansion and contraction or wind loads.
6、The flatness of the keel system fixed with aluminum plate is low
Reason analysis: The low flatness of the keel system fixed with aluminum plate will have a significant impact on the flatness of the aluminum plate wall. Insufficient flatness of the keel system can lead to local unevenness of the aluminum plate after installation, mainly manifested as wavy or uneven shapes. This problem not only affects the aesthetic appearance of the building, but may also cause aluminum plates to deform more easily under external forces such as wind loads and temperature changes. In addition, the issue of keel flatness can accumulate errors during installation, further exacerbating the insufficient flatness of the aluminum plate. Therefore, ensuring the high flatness of the keel system is a key link in ensuring the overall quality of the aluminum curtain wall (Figure 6).
Figure 6: The flatness of the aluminum plate fixed keel system must be strictly controlled
Solution: Control the flatness of the keel;
7、Unreasonable design of installation nodes
Reason analysis: Common connections for metal plates include corner plate connections, fixed distance pressure plate connections, and hanging connections. Corner plate connections have a relatively simple structure and are the most common and cost-effective method, but they are not conducive to absorbing temperature deformation. Aluminum plates generate stress under temperature and do not release it, resulting in aluminum plate deformation; It is highly likely to cause metal panels to arch or collapse, affecting the appearance of the building.
Solution: Try to minimize the use of corner piece connections and adopt a hanging system (Figure 7). The internal stress on the aluminum plate surface is shown in the following figure.
Figure 7 Method of hanging aluminum plate transverse section nodes
(Note: The attached frame may not be full-length, but of course, the edge stiffness of full-length aluminum plates is the best. The advantage of hanging is that the aluminum plates are floating and can be deformed. The length of the pressure plate is 50mm, the width of the pressure plate is 35mm, the thickness is 3.5mm, and the spacing between the pressure plates is 350mm.)
8、Aluminum plate surface treatment selection defects
Reason analysis: Surface treatment methods such as glossiness, film thickness, frosted surface, or diffuse reflective coating on aluminum panels have a significant impact on the flatness of aluminum curtain walls. Aluminum plates with higher glossiness usually have a smoother microstructure, but excessively thick coatings may cause surface deformation due to uneven curing shrinkage or thermal expansion and contraction. Although sand surfaces or diffuse reflective coatings can reduce specular reflection and improve visual uniformity, improper process control may mask small unevenness or produce particle like and ripple effects, affecting overall flatness. Therefore, a reasonable surface treatment process and strict quality control are the key to ensuring the flatness of aluminum curtain walls.
Solution: To address the impact of aluminum plate surface treatment on the flatness of curtain walls, the uniformity of coating thickness should be strictly controlled to avoid deformation caused by curing shrinkage or thermal expansion and contraction; Reasonably choose glossiness, such as using low reflectivity aluminum plates (matte) to ensure high gloss treatment for high flatness areas, while optimizing the sanding and diffuse reflection coating processes to prevent the generation of graininess or ripples. During the construction process, it is necessary to strengthen the protection of the aluminum plate surface, avoid scratches or collisions, and control the construction environment temperature to reduce the impact of temperature changes on the coating. Through these measures, the flatness and overall quality of aluminum panel walls can be effectively improved.
9、Insufficient technical level and sense of responsibility of the construction team
Reason analysis: Insufficient technical disclosure, poor measurement and installation accuracy, outdated and aged operating equipment, inadequate supervision of the construction process, non-standard operation, and poor awareness of finished product protection. These issues can lead to uneven installation of the keel, unstable fixation of the aluminum plate, surface scratches or collision deformation, etc., thereby affecting the flatness and overall quality of the aluminum plate curtain wall, as shown in Figure 8.
Figure 8: Workers install aluminum plates on site
Solution: Strengthen technical training and sense of responsibility education for construction personnel, select skilled installation teams, strictly manage construction and quality supervision, ensure standardized and refined construction processes, and guarantee the flatness and aesthetics of aluminum panel walls.
10、Poor protection during transportation and on-site storage
Cause analysis: During transportation, aluminum plates are prone to scratches, deformation, or surface damage due to collisions, compression, and vibration, which can affect the subsequent installation flatness. After arriving at the site, if stored improperly, such as directly stacking on damp ground, not taking rain and moisture prevention measures, not properly placing isolation materials, etc., it may cause the aluminum plate to become damp, deformed, corroded on the surface, or damaged by other objects.
Figure 9: Proper packaging and protective measures should be taken during the transportation of aluminum plates
Epilogue
The problem of insufficient flatness of aluminum curtain walls has complex causes, involving multiple factors such as design, materials, and construction. By optimizing the facade division, selecting materials reasonably, clarifying the design of stiffeners, increasing the height of folded edges, controlling the flatness of the keel, improving installation nodes, optimizing surface treatment processes, strengthening construction management, and ensuring transportation and storage protection, the flatness of aluminum curtain walls can be effectively improved. All parties need to collaborate and strictly control the design from the source to the construction details to ensure construction quality, thereby guaranteeing the aesthetics and service life of aluminum curtain walls and providing strong guarantees for the quality of building facades.