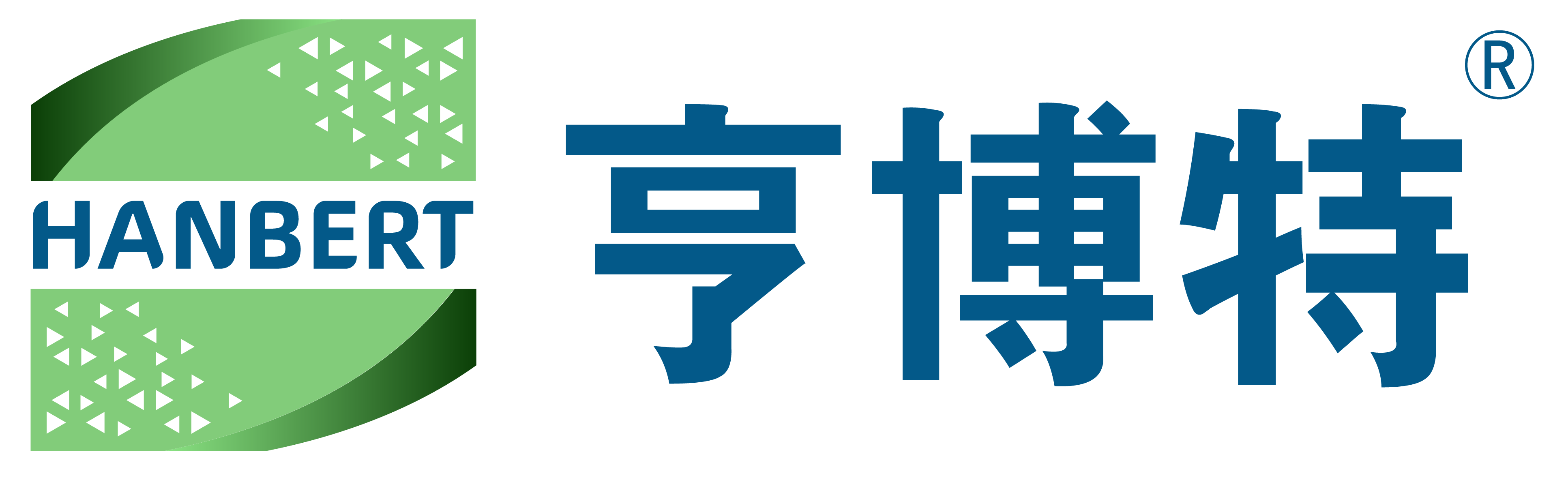
1.Air entered during glue injection
Silicone weather proofing glue "is generally injected at the construction site, and the operating conditions are poor. When workers stand on the foot stand to inject glue, the uniformity of glue injection is not easy to master, and air is easy to enter the glue seam. After applying glue, the surface of the glue seam is scraped and polished. The cushion rod inside the glue seam is generally closed hole polyethylene foam rod, and the air in the glue seam is not easy to overflow. After the air for glue seam trimming is compressed, there will be outward uplift tension. The weather proofing glue seam is generally wide and thin, and the weather proofing glue that provides high displacement ability is low in hardness. The glue is soft before curing, and the uplift tension of compressed air will slowly support the glue seam Foaming. This phenomenon is more likely to occur in the application of weather resistant adhesives that can provide+25% or more of the seam displacement capacity. On the contrary, some weather resistant adhesives with lower displacement capacity have higher hardness and are thicker before curing. The solemn tension of compressed air wrapped in the glue seam is not easy to bubble the glue support. So, the more weather resistant adhesive that can provide high displacement ability, the more attention should be paid to the uniformity of the injection when injecting. Vertical glue joints can generally be glued from bottom to top. It can overcome some foaming phenomena. More importantly, it is the proficiency and sense of responsibility of the work operator.
2.The interface is damp during glue injection
When working outdoors, we often encounter rain, especially in summer in the south. It rains almost every day. If the interface is wet after rain, glue will be injected directly. When the sun shines on the bonding substrate and glue joints, the temperature inside the interface will rise, and the moisture inside the glue joints will evaporate, which will blister the uncured and soft glue. Sometimes the polyethylene foam cushion rod is wet, which will also cause the glue joints to blister. Therefore, during construction, one should not blindly pursue progress. Wait until the interface is dry before injecting glue to avoid the above situation.
3.Deflate the foam rod
Generally, the cushion rod inside the glue seam is closed cell high foaming polyethylene foam rod. Due to improper extrusion during placement, the internal air bag breaks and air is released. When the glue is just injected, there will be bubbles or bulges. The solution to this problem is to cut the foam rod and cut it to the inside. Second, open cell foam rod or polyethylene foam rod is used to overcome the above situation. On the other hand, there are many alcohol types of weather proofing adhesive, and alcohol type weather proofing adhesive will release ethanol when curing, and ethanol will react with some foam rods, such as foaming when silicone weather proofing adhesive is used in a construction site. If another oxime weather resistant glue is used for injection, there will be no foam. In this case, the problem can be solved by changing the foam rod or glue.
4.Exposure to sunlight before the adhesive is cured
Silicone adhesive should not be exposed to direct sunlight before curing, especially when it is just injected. This can cause honeycomb like bubbles to appear inside the adhesive seam, leading to external bulges. This situation is more pronounced when using alcohol based silicone adhesive. This situation is not easy to overcome during the hot summer construction. When using glue injection, avoid direct sunlight to overcome some foaming phenomena. The specific method is to inject glue on the west or north side of the building in the morning, and inject glue on the east or south side of the building in the afternoon. After injection, the glue has solidified for a period of time, and the surface has already formed a crust. When exposed to sunlight again, it has a certain resistance ability and can overcome some foaming phenomena.
5.The surface temperature of the substrate is too high
When silicone adhesive solidifies, the temperature of the bonding material should not exceed 50 ℃, which has been recognized by most silicone adhesive manufacturers. Injecting adhesive when the surface temperature of the substrate exceeds 50 ℃ can cause foaming in the adhesive joint. This situation can be encountered in weather resistant joint filling of metal panel walls. In the hot summer, when the sun shines on metal plates, especially aluminum plates, the surface temperature can reach 80 ℃. At this time, injecting glue can easily cause bubbles in the glue joints. So it is advisable to inject glue in the latter half of the afternoon or on cloudy days to improve the above situation.
6.There is a large temperature difference between day and night, and the interface experiences significant thermal expansion and contraction
This situation is more likely to occur when injecting glue into aluminum curtain walls. Aluminum is a material with a high coefficient of expansion. In the northern regions of China during spring or autumn, the temperature is high day and night, and when the sun shines directly on the aluminum plate at noon, the surface temperature can reach as high as 60-70 ℃. At night, the temperature drops to around 10 ℃. Large aluminum plates also have more thermal expansion and contraction, and the interface displacement is large. After the weather resistant adhesive is embedded, the actual displacement of the interface is borne by the adhesive joint. During the curing process, excessive and repeated expansion and contraction displacement can cause the adhesive joint to bubble. Therefore, when injecting adhesive, avoid the strongest direct sunlight at noon to improve some of the above-mentioned bubble phenomena.
7.The spring climate in northern regions is dry
Silicone sealant needs to utilize moisture in the air to polymerize into elastic sealing material. The temperature in the air is closely related to the curing rate. The climate in northern China is very dry in spring, and the curing time of silicone sealant is very long after injection. The silicone sealant before curing is easily affected by the external environment, providing opportunities for various foaming phenomena.