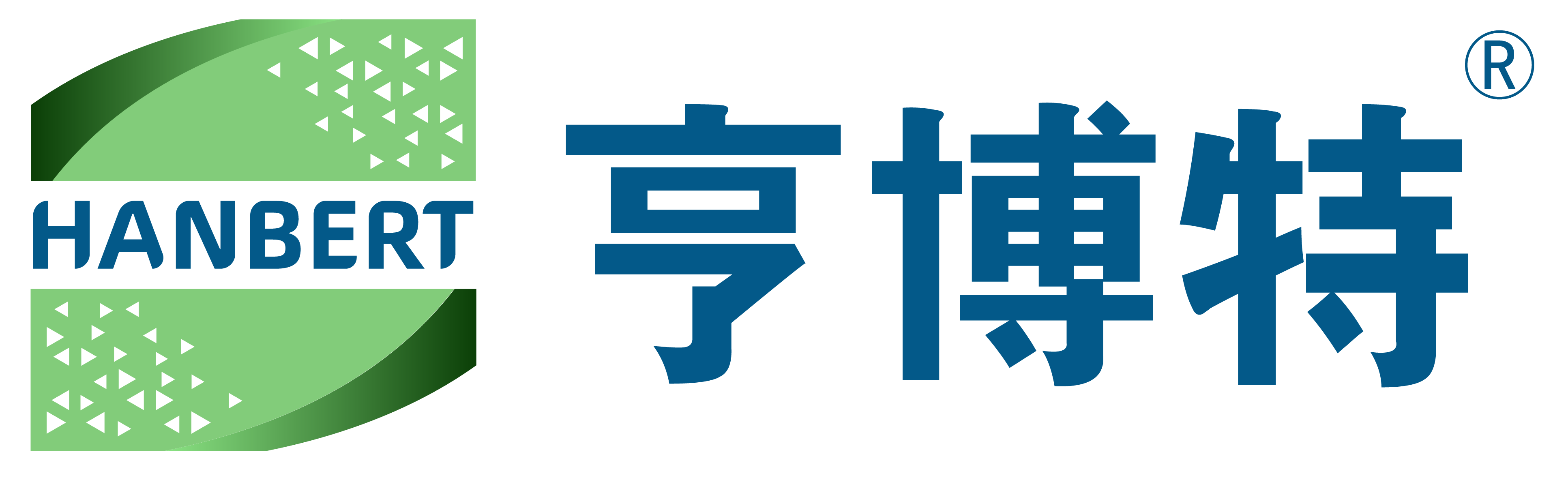
China's building profiles and curtain wall metal panels have become a world-class production powerhouse, from learning to leading, from processing equipment to technological level.
This inevitably relies on the support and empowerment of "surface treatment technology"!
Good profiles and plates require surface treatment as the key, and there are so many processes involved Is the boring definition obscure and difficult to understand? This article has compiled a "complete set of diagrams" for everyone, using text and animation to help you understand 30+surface treatment processes in seconds!
Expectation: To provide valuable technical references for metal material production enterprises, and to enable architects and property owners to have a more three-dimensional understanding of the cost composition of different processes; It also provides more theoretical basis for the selection and application of curtain wall design, construction enterprises, and door and window manufacturers.
PVD, also known as Physical Vapor Deposition, refers to the use of low voltage and high current arc discharge technology under vacuum conditions. It utilizes gas discharge to evaporate the target material and ionize both the evaporated substance and gas. With the acceleration effect of an electric field, the evaporated substance and its reaction products are deposited on the workpiece.
Mechanical polishing is a polishing method that obtains a smooth surface by cutting and plastic deformation of the material surface to remove the raised parts after polishing.
Chemical polishing "is a method that relies on the selective dissolution of uneven areas on the surface of the sample by chemical reagents to eliminate wear marks, etch and level.
Electrolytic polishing "is actually a method of polishing metal surfaces using the principle of electrochemical anodic dissolution.
Spraying is a coating method that uses a spray gun or disc atomizer to disperse into uniform and fine mist droplets under pressure or centrifugal force, and apply them to the surface of the object being coated.
Powder spraying is the process of applying powder coating onto the surface of a workpiece using a powder spraying device (electrostatic sprayer). Under the action of static electricity, the powder is uniformly adsorbed onto the surface of the workpiece, forming a powdery coating.
Electroplating is the process of using the principle of electrolysis to deposit a thin layer of other metals or alloys on the surface of certain metal or other material components.
Anodizing "refers to the process in which aluminum and its alloys form a layer of oxide film on aluminum products (anodes) under the action of external current in the corresponding electrolyte and specific process conditions.
Electrophoretic coating is a process in which charged coating ions move to the cathode under the action of voltage applied to the anode and cathode, and react with alkaline substances generated on the cathode surface to form insoluble substances, which deposit on the surface of the workpiece.
Micro arc oxidation, also known as microplasma oxidation, is the process of growing ceramic film layers mainly composed of matrix metal oxides on the surfaces of aluminum, magnesium, titanium and their alloys through a combination of electrolyte and corresponding electrical parameters, relying on the instantaneous high temperature and high pressure generated by arc discharge.
Metal wire drawing is a surface treatment method that forms lines on the surface of workpieces through grinding, achieving a decorative effect.
Blue burning is the process of filling the entire body with colored glaze and then baking it in a blast furnace at a temperature of approximately 800 ℃. The colored glaze melts from a sand like solid into a liquid, and after cooling, it becomes a brilliant colored glaze fixed on the body. At this point, the colored glaze is lower than the height of the copper wire, so it needs to be filled again and sintered four or five times continuously until the pattern is filled to be level with the wire cutting pattern.
Shot peening is a cold working process that uses pellets to bombard the surface of a workpiece and implant residual compressive stress to enhance its fatigue strength.
Sandblasting is the process of cleaning and roughening the surface of a substrate using the impact of a high-speed sand flow. Compressed air is used as the driving force to form a high-speed jet beam that sprays materials (copper ore, quartz sand, diamond sand, iron sand, Hainan sand) onto the surface of the workpiece to be treated, causing changes in the appearance or shape of the outer surface of the workpiece.
Etching is a technique of removing materials through chemical reactions or physical impacts. Etching, also known as photochemical etching, refers to the process of removing the protective film from the area to be etched through exposure, plate making, and development. During etching, it comes into contact with a chemical solution to achieve the effect of dissolving and corroding, forming concave convex or hollow shapes.
IMD, also known as In Mold Decoration, is an internationally popular surface decoration technology. It consists of a surface hardened transparent film, a printed pattern layer in the middle, an injection molded layer on the back, and ink in the middle, which can make the product resistant to friction, prevent scratches on the surface, and maintain a bright color for a long time without fading.
OMD Out Mold Decoration, abbreviated as OMD, is a decorative technology that integrates visual, tactile, and functional display of IMD extensions. It is a 3D surface decoration technology that combines printing, texture structure, and metallization characteristics.
Laser engraving, also known as laser engraving or laser marking, is a process of surface treatment using optical principles. Using laser light to carve permanent marks on the surface or inside transparent materials.
Electric discharge machining (EDM) is a special machining method that uses the electric erosion effect generated by pulse discharge between two poles immersed in a working fluid to remove conductive materials. It is also known as discharge machining or electric erosion machining, abbreviated as EDM in English. Tool electrodes commonly use corrosion-resistant materials with good conductivity, high melting point, and easy processing, such as copper, graphite, copper tungsten alloy, and molybdenum. During the machining process, there is also wear on the tool electrode, but it is less than the amount of metal removed from the workpiece, and even close to zero wear.
Laser flower biting uses high-energy density laser to react with the surface of steel, forming snake skin/corrosion lines/pear ground or other forms of patterns.
Pad printing is one of the special printing methods, which uses steel (or copper, thermoplastic) gravure printing and a curved pad head made of silicone rubber material. The ink on the gravure printing is dipped onto the surface of the pad head, and then pressed down onto the surface of the desired object to print text, graphics, etc.
Screen printing is the process of stretching silk fabrics, synthetic fiber fabrics, or metal wire mesh onto a frame, and using manual coating or photochemical plate making methods to produce screen printing plates.. Modern screen printing technology uses photosensitive materials to create screen printing plates through photographic plate making methods (making the screen holes in the graphic and textual parts of the screen printing plate through holes, rather than blocking the screen holes in the non graphic and textual parts). During printing, the ink is transferred to the substrate through the mesh holes of the graphic and text parts by the pressure of the scraper, forming the same graphic and text as the original.
Direct thermal printing refers to a method of applying a thermal sensitive agent onto paper to make it a thermal recording paper. The thermal recording paper undergoes physical or chemical changes in the substance (color developer) under the action of heat to obtain an image.
The principle of heat transfer printing is to print digital patterns on specialized transfer paper with special transfer ink through a printer, and then use a dedicated transfer machine to accurately transfer the patterns to the surface of the product at high temperature and high pressure, completing the printing of the product.
Due to the fact that the graphic and non graphic parts of planographic printing are on the same plane, in order to distinguish between the pattern and non pattern parts of the printing plate, the principle of oil-water separation is used. Firstly, the water supply device of the printing plate component supplies water to the non graphic part of the printing plate, thus protecting the non graphic part of the printing plate from ink wetting.
Then, the ink supply device of the printing component supplies ink to the printing plate. As the non graphic parts of the printing plate are protected by water, ink can only be supplied to the graphic parts of the printing plate. Finally, the ink on the printing plate is transferred to the coating, and then the pressure between the coating roller and the impression cylinder is used to transfer the ink on the coating to the substrate, completing a printing process. Therefore, lithography is an indirect printing method.
Curved surface printing is the process of first placing ink into an engraved intaglio with text or patterns, then copying the text or patterns onto the curved surface, transferring the text or patterns onto the surface of the molded product using the curved surface, and finally curing the ink through methods such as heat treatment or ultraviolet light irradiation.
Hot stamping, commonly known as "hot stamping", refers to the process of hot stamping text and patterns made of colored foil or other materials on the first or fourth cover and back of a hardcover book, or using hot pressing methods to imprint various convex and concave book titles or patterns.
Water transfer printing is a type of printing that uses water pressure to hydrolyze polymer onto transfer paper/plastic film with colored patterns. The process includes the production of water transfer printing paper, soaking of the paper, transfer of patterns, drying, and final product.
The flat screen printing mold is a polyester or nylon mesh (pattern) fixed on a square frame with hollow patterns. The patterned areas on the pattern board can be penetrated by the color paste, while the areas without patterns are closed with a polymer film layer to seal the mesh. When printing, the pattern is tightly pressed onto the fabric, and the pattern is filled with color paste. A scraper is used to scrape and press back and forth, allowing the color paste to penetrate the pattern and reach the surface of the fabric.
Rolling is also known as calendering. The final process of heavy leather finishing. The finishing process of using the plasticity of fibers under mixed heat conditions to flatten or create parallel fine diagonal lines on the surface of fabrics, in order to enhance their luster. After the material is fed in, it is heated and melted, then shaped into sheets or films, and then cooled and rolled up. The most commonly used rolling material is polyethylene oxide.