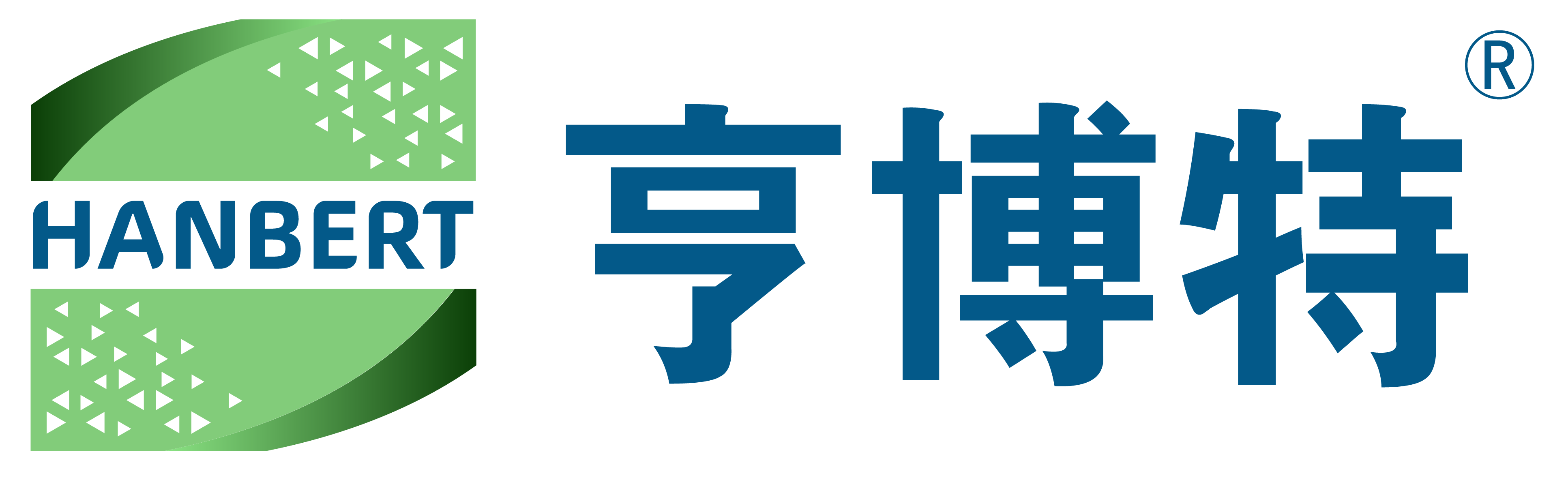
For a long time, architects have regarded plastic polymer materials as secondary building materials. Compared to materials such as glass and metal, plastic polymers have been regarded as inferior building materials in the construction industry. It can be used as a high-performance kitchen material, but it cannot be practically applied to the entire building.
But with the improvement of material properties brought about by technological advancements, this curse has been changed. One of the widely used fluorinated polymer materials is ETFE membrane. Architects have realized the new aesthetic effect expressed by membrane materials and that they can replace other more expensive transparent and semi transparent materials.
01.
INTRODUCTION
The sheet ETFE membrane structure facade © Iwan Baan
Fluoroplastic film (ETFE) is an emerging building material made by copolymerizing ethylene and tetrafluoroethylene. It is a lightweight, heat-resistant film commonly known as "soft glass" and is currently the strongest fluoroplastic. ETFE has greatly improved its radiation resistance, mechanical properties, and processing performance while maintaining the excellent heat resistance, chemical resistance, and electrical insulation properties of PTFE.
In the 1990s, architect Nicholas Greenshaw innovatively applied ETFE membrane on a large scale to the Eden Project in the UK. This material gained recognition from many architects, and with its application in the 2008 Olympic project Water Cube (National Aquatics Center), it attracted widespread attention in China, and its use in architecture has also been increasing.
02.
MATERIAL PERFORMANCE
The sheet ETFE membrane structure facade © Iwan Baan
·Lightweight and high-strength
The ETFE density is 1.73-1.77g/cm3, and the weight of ETFE film per unit area is extremely light, only 1% of the glass mass of the same area. However, ETFE film has good toughness, ductility greater than 400%, high tensile strength, and is not easily torn. According to tests, the tensile strength of a 0.2mm thick film can reach 500 N/5cm, and the tensile strength can reach about 1200 N/5cm, which is nearly twice that of PTFE.
·High transmittance
The visible light transmittance of ETFE film is as high as 95%, and the ultraviolet transmittance is as high as 94%. And the attenuation is very slow, and after 10-15 years of use, it can still maintain above 90%.
Transparent ETFE film, as a material used after inflation, can control the transparency of the film through screen printing dots, adjust the shading and transparency, and effectively utilize natural light; It can simultaneously provide insulation and energy savings by controlling the amount and even the type of gas filled.
The sheet ETFE membrane structure facade © Iwan Baan
·Good adaptability
ETFE film can be processed into almost any size and shape, and can be prefabricated into thin film airbags. It can be assembled and inflated on site, with no wet operation and convenient construction and maintenance.
·ETFE film has strong weather resistance and excellent corrosion resistance to acids, alkalis, chemicals, and most solvents. It can maintain material integrity in harsh environments and has a service life of up to 25-30 years.
·Anti static, light dust pollution
ETFE membrane has excellent self-cleaning function, and ash is not easily adsorbed on its surface.
03.
MATERIAL CLASSIFICATION
Detail of inflatable membrane structure facade © Iwan Baan Property: Permanent
The membrane structure in the building envelope can generally be divided into inflatable membrane structure, tensioned membrane structure, and skeleton membrane structure according to the forming method and stress characteristics of the membrane structure.
·Inflatable membrane structure
The inflatable membrane structure is based on ETFE membrane material technology, which combines two or more layers of membranes through hot melt welding to form a closed air cushion. Its periphery is clamped in a frame made of aluminum alloy or other materials, and the frame is fixed to the main structure of the building. In the air cushion, clean and dry air that has been filtered and dehumidified is filled through the reserved valve port to create an inflatable membrane structure system. This inflatable form is commonly used in the peripheral protection structure of buildings.
ETFE inflatable membrane structure relies on the strength of the membrane material itself and the internal pressure of the air cushion to jointly bear external loads. In order to improve the insulation effect of ETFE inflatable membrane, the number of layers can be increased from two to three or four. Considering the functional use of buildings, the light transmittance of membrane materials should be reasonably controlled, and measures such as colored or printed dots and patterns can be adopted. The inflation control system can also be intelligently controlled.
Detail of tensioned membrane structure facade © Richard Bryant
The membrane structure used in buildings is mainly a tensioned cable membrane structure system. The tensioned membrane structure is composed of membrane materials, steel cables, and pillars, which use steel cables and pillars to introduce tension into the membrane materials to achieve stability.
Tensioning film is a stable load-bearing system composed of the tension force and special geometric shape of the film material itself. The membrane can only withstand tension and cannot be compressed or bent. Its surface stability is maintained by mutually opposite curvatures, so it needs to be made into a concave convex spatial surface, which is commonly known as a spatial membrane structure.
The tensioned membrane structure is usually constructed by laying steel cables along the edges of the membrane, applying tension to the cables, and driving the membrane to tension and form, generating sufficient prestress. Therefore, it is called a tensioned cable membrane structure. If the area of the membrane is too large and the membrane itself cannot withstand the expected load, reinforced steel cables can be added in the middle of the membrane to improve its wind resistance.
The tensioned cable membrane structure can be made into any complex curved shape according to the needs, reflecting the beauty of natural smoothness. There are also various colors of membrane materials to choose from to adapt to the surrounding environment and meet the requirements of building effect; Moreover, the membrane structure is lightweight and generally does not require a large supporting structure, which is an advantage that other building materials cannot match
·Skeleton membrane structure
Skeleton membrane structure facade details © Xingzhi Image - Li Yi
Skeleton membrane structure is a rigid skeleton made of steel or other materials, which has natural stability and integrity. The membrane is tensioned and placed on the skeleton to form a skeleton membrane structure, with shapes including flat, single curved, and hyperbolic represented by saddle shape.
The significant feature of skeleton membrane structure is that the membrane is not a necessary structural unit to maintain the existence of the structural system, but it is not simply used to cover the roof system, but fully utilizes its building lighting function and high-strength stress characteristics.
Although the effect of pre tension on the morphology of skeleton membrane structures is not as significant as that of tensioned membranes, sufficient tension must be introduced to ensure the structural stress characteristics and avoid significant vibration of the membrane surface under wind loads, which can cause relaxation and depression of the membrane surface. The skeleton is generally exposed on the inside of the membrane, and the transparency of the membrane highlights the indoor visual effect of the skeleton. Therefore, the layout, form, material, nodes, etc. of the skeleton are the focus of design considerations, and should strive for simplicity and aesthetics.
04.
INSTALLATION REQUIREMENTS
·Thermal insulation and waterproofing
The secondary keel of the ETFE roof assembly system adopts the form of "gutter+waterproof insulation layer". The ETFE membrane fixture is hooked on the edge of the steel gutter, which serves as the main load-bearing component. Self tapping and self drilling nails play a fixing role, making the stress in this area more reasonable. Specific composite adhesive strips are used at the connection to prevent rainwater from leaking into the room.
At the same time, the tip of the self tapping self drilling nail is exposed to the outside, and even if there is water leakage at the self tapping self drilling nail hole, the water droplets will eventually flow outside. High quality waterproof and insulation materials are used in the gutter to better utilize the waterproof function of the roof.
·Node waterproofing
ETFE tension film generally does not adopt the form of setting steel cables around it and tensioning the film through steel cables. Instead, a single-layer ETFE film is cut into the desired shape, and edge ropes are set around it, and then clamped with a special aluminum alloy fixture. By applying tension on the surrounding fixtures, the membrane material is fully tensioned, and external loads are resisted by the internal prestress of the membrane material.
05.
ARCHITECTURAL CASE
Eden Garden, Cornwall, UK © Hufton+Crow
The botanical Eden project designed by Grimshaw for Devonshire in southwest England can be considered one of his most representative works. This once abandoned quarry now features a carefully designed landscape and a cutting-edge greenhouse for collecting and displaying precious plants and specimens. This project is the most successful modern interpretation of the Buckminster Fowler geodesic dome concept.
The curved roof of Eden is made of lightweight materials, and a semi transparent ETFE film material is laid in the middle of the skylight. Under certain lighting conditions, these large greenhouses sometimes look like giant, shiny soap bubbles, sometimes like insect compound eyes, and at first glance, they may seem like a pile of giant frog eggs or giant insect larvae. The curved roofed building imitates various ecological environments on Earth, showcasing different biological communities and accommodating thousands of exotic flowers and grasses.
National Aquatics Center Venue - Water Cube © Zhang Liang
The exterior of the Beijing National Aquatics Center resembles an ice crystal shaped cube, with a simple and modern design. The internal and external facial mask structure of Water Cube consists of 3065 air pillows, of which the smallest is 1-2 square meters, the largest is 70 square meters, the coverage area is 100000 square meters, and the developed area is 260000 square meters.
These air pillows are highly sustainable buildings with a semi transparent ETFE outer membrane, weighing only one percent of the same size glass, like an insulated greenhouse. About 20% of the solar energy is used to raise the temperature of the swimming pool and indoors. These semi transparent and recyclable films provide ample daylight for the Water Cube, coupled with appropriate artificial light sources inside, giving people a visual enjoyment.
Guangzhou Infinitus Plaza © Felix Amiss /Liang Xue
Zaha Hadid designed Guangzhou Infinitus Plaza, which integrates a building intelligent management system and a sprinkler network powered by photovoltaic systems, can spray atomized particles of collected rainwater onto ETFE membrane roofs above each atrium, and then achieve heat dissipation and cooling through evaporation.
Each semi transparent double-layer ETFE membrane roof contains a 60cm compressed air. When the outer surface temperature of ETFE membrane rises to 35 ℃ through solar radiation, the sprinkler network will be activated. Spraying for 3-4 minutes every half hour can raise the surface temperature of the membrane to 14 ℃, effectively reducing the indoor temperature by 5 ℃. This will also reduce the energy demand of rooftop solar hot water systems.
Suizhou South Station © Shi Zheng/front, Ding Shuo/back
In the design of Suizhou South Station, the architect abstracted and reconstructed the ginkgo leaves to obtain the basic "leaf units" that make up the space. The natural curves with rich rhythm and the light and agile architectural form make the interior and exterior spaces of the building seamlessly integrated. The leaf shaped unit integrates architecture, structure, and lighting, and the light passes through the film to slowly reveal the internal structure, like the texture of leaves, symbolizing nature and reflecting the beauty of the structure.
The key to the formation of this spatial effect lies in the performance of the ETFE membrane material covering the outer side of the unit cell. To ensure that the "blades" ultimately form a full and smooth curved surface shape, the project team needs to have extremely precise control over the tension of the cable net system and membrane materials, and complete the design and installation of the spare components of the "blades".
Anaheim Regional Transportation Intermodal Center © John Linden
The flexible station design and master plan of the Anaheim Regional Transport Intermodal Center have expanded the definition of transportation, incorporating it into a larger vision of a more urban and mixed use future, where this station is more than just a station. The inspiration comes from iconic transportation facilities such as Pennsylvania Station in New York City, which changed the public's concept of transportation by serving as a new focal point of the city. Through eye-catching design language, the design team has set the stage for cultural and economic transformation in a key region of Southern California.
The transportation center adopts a high-tech ETFE system to achieve maximum lighting and environmental control. Every aspect of the design carefully considers its energy and environmental performance. The ETFE main shell of the building is combined with operable louvers on the north and south tomb walls, and combined with heating and cooling floor radiation technology, providing a comfortable and natural lighting indoor environment. Through close and continuous collaboration between architects, engineers, and stakeholders, as well as successful use of BIM at all stages, the team was able to reduce the energy consumption of the project by 50%.
Anaheim Regional Transportation Intermodal Center © John Linden