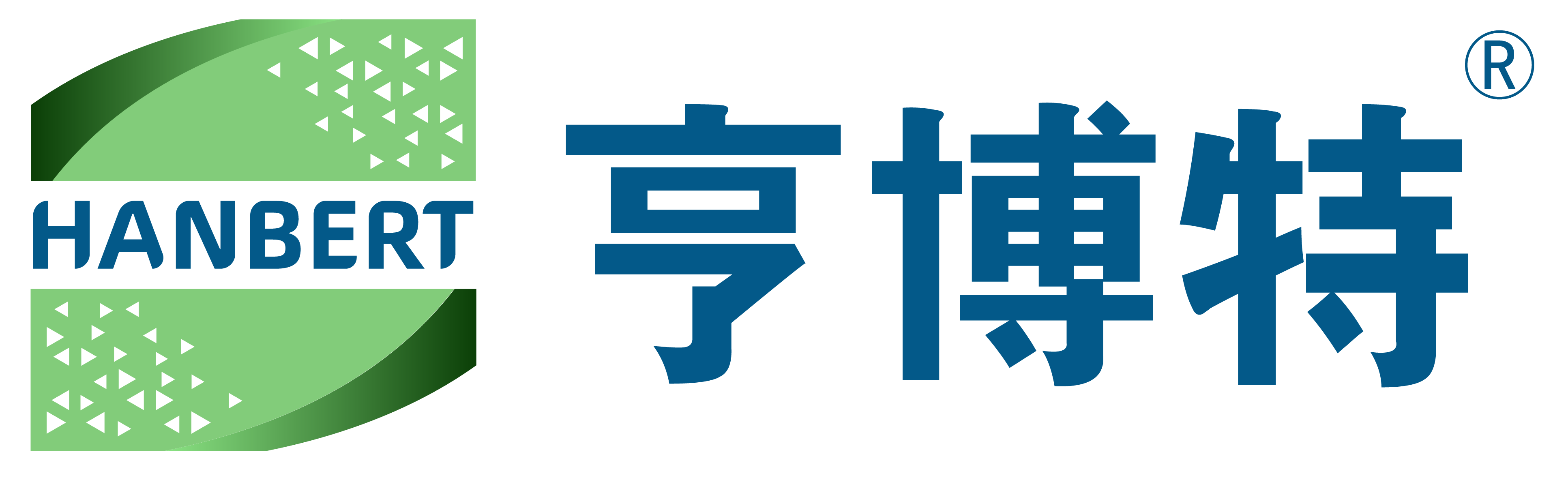
Beijing Daxing International Airport, as the world's largest airport, has a total construction area of 1.43 million square meters and a designed annual passenger throughput of over 100 million people. Its various engineering projects have set a record in the industry. Its interior decoration also demonstrates exquisite craftsmanship, with the large suspended ceiling being the core part. The interior decoration project fully utilizes digital construction technology and carries out construction through full process digital construction.
The departure hall on the fourth floor of the main terminal of Beijing Daxing International Airport and the VIP lounge of China Eastern Airlines cover a total area of 36000 square meters. The "large suspended ceiling" responsible for construction is located in the northwest area of the departure hall on the fourth floor of the core area of the main terminal.
The departure hall on the fourth floor of the main terminal building is composed of a large roof suspended ceiling system, a wall and ground system, a panel edge fence partition system, a floating island system, and a steel connected bridge. The large roof suspended ceiling system consists of a small curvature suspended ceiling, C-shaped columns, and a skylight. Sections of aluminum panels extend from the ground through columns to the edge of the curtain wall and onto the roof truss. Light passes through the skylight, like white ribbons scattered, like auspicious clouds, extremely beautiful. The project department adopted a leading domestic digital construction operation system for the entire process, and completed the scaffolding free installation of the 33160 square meter roof suspended ceiling system in just three months.
Using digital technology to construct a huge "irregular" structure roof suspended ceiling
The steel structure roof truss of the roof suspended ceiling system has a large spatial span and complex wheel relationships. If conventional on-site data collection is used, a large amount of manpower and material resources are required to make templates. Whether it is making templates or manually measuring data, accurate measurement results cannot be achieved. The project department has set its sights on laser 3D scanning technology, which has been widely used in giant "irregular" structures and can precisely solve the measurement and verification problem of large ceiling systems. The project engineer uses a comprehensive 3D laser scanner to scan the entire space of the large ceiling system in all directions, forming a computer 3D model with an accurate coordinate system. The three-dimensional model is compared with the original traditional model to identify the deviation of the on-site structure, and then undergoes post-processing correction to replace traditional on-site verification with modern digital technology, providing important basis for the deepening and adjustment of subsequent models.
After obtaining an accurate coordinate system 3D model, the project department adopted 3D deepening technology to unify the coordinates of the roof truss model and the surface model, and simulated collision problems, conversion layer problems, and installation problems, effectively avoiding problems that may be triggered by future construction. Based on the deepening optimization of the model, the project department innovatively developed a ceiling connection block for the conversion disc. Unlike traditional conversion nodes, the conversion disc has better directionality. The conversion layer module can be turned and fixed on the conversion disc at will, ensuring excellent construction results.
The entire roof large ceiling system consists of more than 20000 small curvature ceiling diffuse reflective aluminum panels. The project team first conducts in-depth simulation of the surface models of aluminum panels in each section, then unifies the mold closing and adjusts the errors between the models. Using engineering professional software, the prefabricated processing drawings of aluminum panels are made, and the centralized ordering of aluminum panels is completed, greatly saving costs and time. Through the digital measurement and installation technology of full station measurement and review, it is easy to determine the installation positioning of over 20000 aluminum plates, ensuring that each component and aluminum plate can be accurately installed.
Innovative construction technology for roof large suspended ceiling system to achieve scaffolding free construction
The application of various digital technologies has laid the foundation for subsequent scaffolding free construction. The project department adopts the method of high-altitude vehicle assisted climbing and aerial platform reverse operation for ceiling construction. Before construction, two life ropes are installed on the web members of the steel structure truss, and a safety net is installed above the lower chord. Construction personnel use the inspection passage on the steel structure truss to reach the installation point, and with the assistance of the ground high-altitude vehicle, the conversion disc and the main frame of the conversion layer are installed.
After the construction of the main frame of the conversion layer is completed, the project department will lay steel scaffolding boards inside the main frame and set up an aerial operation platform for aluminum plate installation. The comprehensive application of the "disc type" conversion node, "three-layer" installation node, and "unit type" aluminum panel decoration panel in the suspended ceiling enables the installation error of components to be reduced layer by layer, while enabling point-to-point installation and leveling construction, ultimately achieving scaffolding free construction of this giant roof large suspended ceiling system.
Nowadays, travelers from all over the world can experience the exquisite and magnificent interior of Daxing Airport.