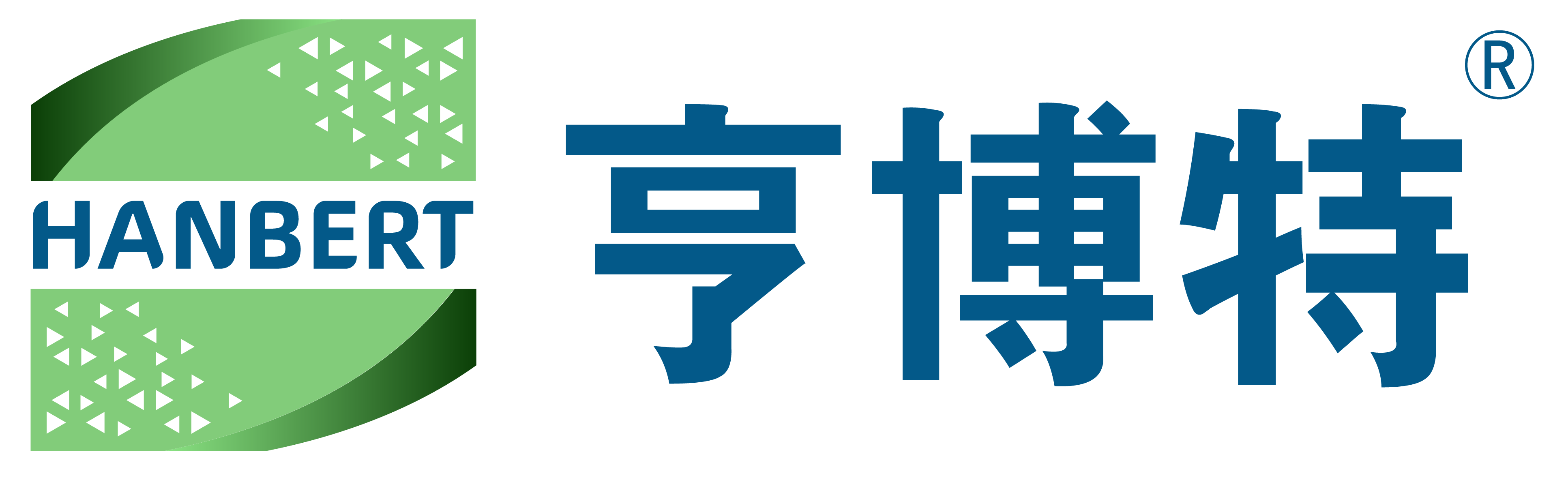
There are many processes for pre-treatment of aluminum spray coating, which can be selected based on specific conditions, such as factory conditions such as spatial location, workpiece materials (cold-rolled plates, hot-rolled plates, galvanized plates, aluminum alloys, fiberglass, etc.), workpiece surface conditions (rust, rust proof oil, impurities), production batch quantity, quality requirements, etc. Different manufacturers adopt different processes, such as the overall process and quality requirements for bus production, which are basically the same. There are generally two types of pre-treatment processes:
01.Pre processing of parts
Typical process flow: pre degreasing → degreasing → water washing | → acid washing → water washing 1 → neutralization → water washing Sichuan → surface adjustment - phosphating - water washing IV - passivation. The manufacturer can make appropriate adjustments according to the actual situation of the factory.
As a pre-treatment for parts, acid pickling and rust removal are essential. But in the pre-treatment process, it is best to separate the corroded parts from the non corroded parts, and acid wash the corroded parts. It is best not to acid wash the non corroded parts.
02.Product pre-treatment
Product pre-treatment is the process of immersing the entire product in a tank solution for surface treatment, which has been adopted by many manufacturers. There are two types of transfer between processes: manual control and automatic control. A more advanced approach is to use PLC program for automatic control, which can achieve automatic transfer between processes. The general process is: degreasing → washing with water → surface adjustment → phosphating → washing with water.
The commonly used equipment for pre-treatment before spraying is a spray type combined cleaning machine, which relies on the mechanical force and chemical action of spraying to complete processes such as degreasing, phosphating, passivation, and cleaning.
The typical processes of a spray type combined cleaning machine include degreasing, water washing, surface adjustment, phosphating, passivation, water washing, and pure water washing.
Its structural feature is that the spray pipes of each process in the pre-treatment production line are arranged in the tunnel, and the spray is provided by the pumps of each liquid tank. There are door panels separating each process to prevent honey liquid. The heating forms of each heating liquid tank include inside and outside the tank. The internal heater includes exhaust pipes, serpentine pipes, corrugated plates, etc; External heaters include tube and plate heaters, etc. Heating media include hot water, steam, thermal oil, etc. There are oil removal systems and slag removal systems respectively installed in the degreasing and phosphating processes. To prevent steam from overflowing from the top of each heating section tunnel and the door opening, exhaust fans are installed at the top of the tunnel.
03.Each process control element is described as follows:
1、Defatting
The degreasing mechanism is achieved through the saponification, solubilization, wetting, dispersion, and emulsification of various oils and fats by degreasing agents, thereby causing the oils and fats to detach from the surface of the workpiece, become soluble substances, or be emulsified, dispersed and uniformly and stably present in the tank liquid. The evaluation of degreasing quality is mainly based on the fact that the surface of the workpiece after degreasing should not have visual grease, emulsion or other dirt, and the surface should be completely wetted by water after washing.
The quality of degreasing mainly depends on factors such as free alkalinity, temperature of degreasing solution, processing time, mechanical action, and oil content of degreasing solution:
(1)Free alkalinity (FAL)
Proper concentration of degreaser is necessary to ensure optimal results. Generally, only the free alkalinity of the degreasing solution needs to be tested. If the FAL is too low, the degreasing effect is relatively poor. If the FAL is too high, it not only causes material waste, but also increases the burden on the subsequent water washing. In severe cases, it can also pollute the surface and phosphating of the subsequent process.
(2)Temperature of degreasing solution
Any degreasing solution has the optimal degreasing temperature, which is lower than the process requirements and cannot fully exert the degreasing effect; Excessive temperature not only increases energy consumption but also brings some side effects. If the degreaser evaporates too quickly and the workpiece is detached from the liquid, the surface drying speed is fast, which can easily cause defects such as rust, alkali spots, and discoloration of the workpiece, affecting the phosphating quality of the subsequent work seat. Automatic temperature control also requires regular verification.
(3)Processing time
The degreasing solution must be in full contact with the oil stains on the workpiece and have sufficient contact reaction time to ensure a good degreasing effect. But if the degreasing time is too long, it will increase the dullness of the workpiece surface and affect the formation of the phosphating film.
(4)The influence of mechanical action
During the degreasing process, mechanical action is used in conjunction with pump circulation or workpiece movement to enhance the degreasing effect and shorten the immersion cleaning time; The speed of spray degreasing is more than 10 times faster than that of immersion degreasing.
(5)Oil content of degreasing solution
As the tank liquid is recycled, the oil content in the tank liquid will continue to increase. When a certain proportion is reached, the degreasing effect and cleaning efficiency of the degreaser will significantly decrease. Even if the high concentration of the tank liquid is maintained by adding chemicals, the cleanliness of the surface of the treated workpiece will not improve. The degreasing solution that has aged and deteriorated must be completely replaced. Product production generally involves timely tank replacement based on the usage time and processing workload of the tank solution.
2、Pickling
During the process of rolling, forming, storage, and transportation, the surface of steel used in product manufacturing may rust. Due to the loose structure of the rust layer, which is not firmly attached to the substrate, and the fact that oxides and aluminum iron can form a primary battery, further promoting aluminum corrosion and quickly damaging the layer, it must be removed before painting. The commonly used product is acid pickling for rust removal, which does not cause deformation of aluminum workpieces. Every corner of the rust can be completely removed, with a fast rust removal speed and relatively low cost.
The quality of pickling is mainly based on the fact that the workpiece after pickling should not have visible oxides, rust, or excessive corrosion. The factors that affect the rust removal effect mainly include:
(1)Free acidity (FA)
Measuring the free acidity FA of the pickling tank is the most direct and effective evaluation method to verify the rust removal effect of the pickling tank. Low free acidity and poor rust removal effect. When the free acidity is too high, the acid mist content in the working environment is high, which is not conducive to labor protection; The surface of aluminum material is prone to "over corrosion" phenomenon, and the cleaning of residual acid is relatively difficult, which can easily lead to subsequent contamination of the tank liquid.
(2)Temperature, time
Most pickling is carried out at room temperature. When using heated pickling, it is generally controlled between 40 ℃ and 70 ℃. Although temperature has a significant impact on the improvement of pickling ability, excessive temperature can exacerbate corrosion of workpieces and equipment, and have a very adverse impact on the working environment. Moreover, on the premise of completely removing rust, the pickling time should be as short as possible to reduce the impact of aluminum corrosion and hydrogen embrittlement. Therefore, during the processing, the temperature of the tank liquid and the processing time of the workpiece should be strictly controlled.
(3)Pollution aging
During the rust removal process, acid will continuously introduce oil stains or other impurities, and the suspended impurities can be removed by scraping; When the soluble iron ions exceed a certain content, the rust removal effect of the tank solution will not only be greatly reduced, but excessive iron ions will also mix with the residual liquid on the surface of the workpiece into the phosphating tank, accelerating the pollution and aging of the phosphating tank solution, seriously affecting the phosphating quality of the workpiece. Generally, the iron ion content in the acid solution should be controlled within 6% -10%. When the control indicators are exceeded, the tank liquid must be replaced.
3、Table tuning
Surface adjustment agents can eliminate the unevenness of the surface state of workpieces caused by alkaline degreasing or acid pickling rust removal, forming a large number of extremely fine crystal centers on the surface of aluminum materials, thereby accelerating the rate of phosphating reaction and facilitating the formation of phosphating film.
(1)The impact of water quality
If the water used in the tank liquid contains severe rust and high calcium and magnesium ion content, it will affect the stability of the surface adjustment liquid. When preparing the tank liquid, a water softener can be added in advance to eliminate the influence of water quality on the surface adjustment liquid.
(2)Usage time
Generally, colloidal titanium salts are used for surface adjustment, which have colloidal activity. When used for a long time or contain a lot of impurity ions, the colloidal activity will be lost. At this time, the stable state of the colloid is disrupted, and the liquid precipitate is layered and flocculent. At this time, the tank liquid must be replaced.
4、Phosphating
Phosphating is a process of chemical and electrochemical reactions to form a phosphate chemical conversion film, and the resulting phosphate chemical conversion film is called a phosphating film. The commonly used coating solution for passenger cars is low-temperature zinc based phosphating solution. The main purpose of phosphating is to provide protection for the base aluminum material and to some extent prevent corrosion of the aluminum material; Used as a primer before painting to improve the adhesion and corrosion resistance of the paint film layer.
Phosphating is the most important part of the entire pre-treatment process, with a complex reaction mechanism and multiple influencing factors. Therefore, the production process control of phosphating tank solution is much more complex compared to other tank solutions.
(1)Acid ratio (ratio of total acidity to free acidity)
Increasing the acid ratio can accelerate the phosphating reaction rate, making the phosphating film thin and fine. However, if the acid ratio is too high, the film layer will be too thin, which can easily cause the phosphating workpiece to hang dust; The acid ratio is too low, the phosphating reaction rate is slow, the phosphating crystals are coarse and porous, the corrosion resistance is low, and the phosphating workpiece is prone to yellow rust. Generally speaking, the acid ratio requirements vary depending on the system or formula of the phosphating solution.
(2)Temperature
An appropriate increase in the temperature of the tank solution will accelerate the film-forming speed, but if the temperature is too high, it will affect the change in acid ratio, thereby affecting the stability of the solution. At the same time, the crystal nucleus of the membrane layer is coarse, and the amount of slag discharged from the tank solution will increase.
(3)Sediment volume
As the phosphating reaction continues, the amount of sediment in the tank liquid will gradually increase. Excessive sediment will affect the interface reaction on the surface of the workpiece, causing the phosphating film to flower, hang ash seriously, and even fail to form a film. Therefore, the tank liquid must be timely poured according to the amount of workpiece processed and the usage time, for slag and sediment removal.
(4)Nitrite NO-2 (accelerator concentration)
NO-2 can accelerate the phosphating reaction rate, improve the density and corrosion resistance of the phosphating film. When the content is too high, the film layer is prone to white spots or discoloration; If it is too low, the film forming speed is slow, and the phosphating film is prone to yellow rust.
Sulfate SO2-4
Excessive concentration of pickling solution or poor water washing control can easily lead to an increase in sulfate ions in the phosphating tank solution. Excessive sulfate ions can slow down the phosphating reaction rate, resulting in coarse and porous grains of the phosphating film, severe ash deposition, and reduced corrosion resistance of the phosphating film.
(6)Ferrous ion Fe2+
When the content of ferrous ions in the phosphating solution is too high, it will reduce the anti-corrosion ability of the phosphating film at room temperature; It will cause the grain size of the medium temperature phosphating film to become coarse, the surface to float white ash, and the anti-corrosion ability to decrease; It will increase the amount of sediment in the high-temperature phosphating solution, make the solution turbid, and at the same time, increase the free acidity.
5、Passivation (sealing)
The purpose of passivation is to seal the pores of the phosphating film, improve the corrosion resistance of the phosphating film, especially improve the overall adhesion and corrosion resistance of the paint film. At present, two methods are generally used: chromium containing treatment and chromium free treatment. However, some use alkaline inorganic salt passivation (mostly containing phosphates, carbonates, nitrites, phosphates, etc.), which seriously damage the long-term adhesion and corrosion resistance of the paint film.
6、Water washing
The purpose of water washing is to remove residual liquid from the previous groove on the surface of the workpiece. The quality of water washing can directly affect the phosphating quality of the workpiece and the stability of the entire groove. The general control of water washing tank liquid includes the following:
(1)The amount of sludge residue should not be too high. Excessive content can easily lead to dust hanging on the surface of the workpiece;
(2)The surface of the tank liquid should be free of suspended impurities. The general water washing method adopts overflow water washing to ensure that the surface of the tank liquid is free of suspended oil stains or other impurities;
(3)The pH value of the tank liquid should be close to neutral. Both high or low pH values can easily cause the tank liquid to cross flow, thereby affecting the stability of the subsequent tank liquid.